Современные древесные материалы. Что такое древесный материал
Древесные материалы и их применение в строительстве
Дерево применяется в строительстве очень давно, но современная промышленность дали возможность использовать более совершенные материалы.
Многослойная фанераСлово “Фанера” это французское слов, которое в дословном переводе означает накладывать. Действительно сам материал состоит из 3 и более слоев древесного материала, которые соединены связующим веществом искусственного происхождения. Как правило, древесный материал — это шпон дерева, тонкие слои березы, сосны.
При изготовлении фанеры листы шпона укладывают в перпендикулярном расположении древесных волокон. За счет этого тонкий строительный материал получает достаточно высокую прочность. Кроме того фанера сохраняет форму при изменении влажности и температуры в помещении, что выгодно отличает ее от натуральной древесины. Связующим материалом выступает различного рода клей, который зависит от требуемых характеристик фанеры. От клея зависит водостойкость фанеры.
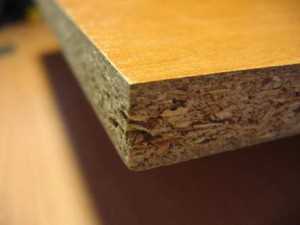
Следующий древесный материал, который используется для обшивки стен, потолка и пола -ДВП. При изготовлении этих плит используются стружки, которые проходят машинное прессование с добавлением клея. Минусом плит ДВП является низкая сопротивляемость к влажности, поэтому их преимущественно используют в сухих помещениях. Кроме того ДВП плита достаточно тяжелая. При выборе таких плит следует обращать внимание на сертификат качества от производителя, в частности какой клей использовали при изготовлении плиты. Назначение ДВП — отделка, выравнивание, звуко и теплоизоляция. ДВП широко используют при изготовлении мебели. Из ДВП выполнены все ненесущие элементы каркасных зданий.
OSB плита. С развитием технологии появилась ОСП (см подробнее тут http://osbplyta.ru/buying.html), цена которой немного выше ДВП, но при этом она обладает рядом преимуществ. OSB (осп) — жто ориентированно-стружечная плита, которая изготовлена также методом прессования, но в данном случае прессование является горячим и трехслойным. При этом щепы верхнего и нижнего слоя ориентируется вдоль длинной стороны готовой плиты, а щепа внутреннего слоя расположена перпендикулярно. Кроме того при изготовлении плиты используется как длинная переплетенная между собой щепа, так и крупноразмерная спрессованная (на внешних сторонах). Так же как и в случае с фанерой, получается материал, который не боится влаги, перепадов температур.
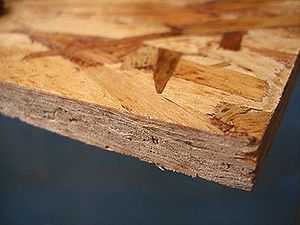
К преимуществам OSB плиты следует отнести:
1. высокую прочность.
2. возможность сохранять первоначальную форму.
3. возможность использования во влажных помещениях и открытом воздухе.
4. относительную легкость механической обработки.
5. отличную звуко и теплоизоляцию.
OSB плиты используются для укладки пола, как выравнивающие элементы. При помощи этих плит можно обустраивать кровлю из гибкой черепицы или других битумных кровельных материалов.
stroy-dom.info
Дерево (материал) - это... Что такое Дерево (материал)?
Древеси́на. В обыденной жизни и технике древесиной называют внутреннюю часть дерева, лежащую под корой. В ботанике под древесиной, или ксилемой, подразумевают ткань или совокупность тканей, образовавшихся из прокамбия или камбия.
Образование древесины
Древесина является одной из составных частей сосудисто-волокнистого пучка и противопоставляется обыкновенно другой составной части пучка, происходящей из того же прокамбия или камбия — лубу, или флоэме. При образовании сосудисто-волокнистых пучков из прокамбия наблюдаются 2 случая: либо все прокамбиальные клетки превращаются в элементы древесины и луба — получаются так называемые замкнутые пучки (высшие споровые, однодольные и некоторые двудольные растения), либо же на границе между древесиной и лубом остаётся слой деятельной ткани — камбий и получаются пучки открытые (двудольные и голосемянные).
В первом случае количество древесины остаётся постоянным, и растение неспособно утолщаться; во втором благодаря деятельности камбия с каждым годом количество древесины прибывает, и ствол растения мало-помалу утолщается. У российских древесных пород древесина лежит ближе к центру (оси) дерева, а луб — ближе к окружности (периферии). У некоторых других растений наблюдается иное взаимное расположение древесины и луба (см. Сосудисто-волокнистые пучки). В состав древесины входят уже отмершие клеточные элементы с одеревеневшими, в основном толстыми оболочками; луб же составлен, наоборот, из элементов живых, с живой протоплазмой, клеточным соком и тонкой неодеревеневшей оболочкой. Хотя и в лубе попадаются элементы мёртвые, толстостенные и одеревеневшие, а в древесине, наоборот, живые, но от этого, однако, общее правило не изменяется существенно. Обе части сосудисто-волокнистого пучка отличаются ещё друг от друга и по физиологической функции: по древесиной поднимается вверх из почвы к листьям так назывываемый сырой сок, то есть вода с растворёнными в ней веществами, по лубу же спускается вниз образовательный, иначе пластический, сок (смотрите Соки в растении). Явления же одеревенения клеточных оболочек обусловливаются пропитыванием целлюлозной оболочки особыми веществами, соединяемыми обыкновенно под общим названием лигнина. Присутствие лигнина и вместе с тем одеревенение оболочки легко узнаётся при помощи некоторых реакций. Благодаря одеревенению, растительные оболочки становятся более крепкими, твёрдыми и упругими; вместе с тем при лёгкой проницаемости для воды они теряют в способности впитывать воду и разбухать.
Заготовка и транспортировка древесины
Переработка древесины
Породы древесины
Ценные породы древесины
Ценность различных пород древесины заключается в их прочности, долговечности и неповторимости рисунка. Такая древесина используется для для изготовления красивой мебели, паркета, дверей, различных предметов интерьера, считающимися элитными, учитывая исходно высокую стоимость и размер усилий, затрачиваемые на ее обработку. В России наиболее распространены следующие породы: дуб, вишня, бук, груша, розовое дерево, махагони, грецкий орех, клён (белый, сахарный, остролистный)[1][2].
Основные эксплуатационные показатели
- Твёрдость — показатель срока службы верхнего слоя древесины. Чем выше твёрдость, тем медленнее идёт износ. Одним из показателей твёрдости является шкала Янка.
- Стабильность и уровень усадки — показывает совместимость различных пород древесины при совместном использовании (в паркете, инкрустациях и т. п.). Также показывает пригодность их использования в различных климатических условиях.
- Степень окисления — показывает изменение цвета древесины под воздействием света. Чем выше степень, тем больше темнеет древесина.
- Выразительность текстуры — влияет на зрительное восприятие человеком. При большей контрастности создаётся больший возбуждающий эффект.
- Стойкость к нагрузкам — способность древесины выдерживать те или иные нагрузки.
Для каждой породы (иногда даже для различных частей дерева) все его свойста могут быть различны, это зависит от различных условий, в которых росло то или иное дерево.
Древесина как строительный и поделочный материал
Пиломатериалы
Деревянные строительные конструкции
Древесина как отделочный материал
- Паркет
- Настенные панели
- Деревянные потолки
- Плинтусы и уголки
- Деревянные окна и двери
Древесина в мебельном производстве
Древесина как поделочный материал
Торговля древесиной
Международные соглашения
См. также
Примечания
Ссылки
Wikimedia Foundation. 2010.
dal.academic.ru
Виды материалов из древесины
Лесоматериалом называют материалы из древесины, сохранившие свою природную физическую структуру и химический состав. Их разделяют на необработанные (круглые) и обработанные (пиломатериалы, колотые лесоматериалы, шпон и др.)
Круглые лесоматериалы – отрезки стволов деревьев с обрубленными сучьями с корой или без коры. В зависимости от диаметра различают:
· Брёвна D = более 12 см
· Подтоварник D = 8 – 11 см
· Жерди D = 3 – 7 см
Круглые лесоматериалы разделяют на 4 сорта. В строительстве применяют преимущественно 2 и 3. По назначению брёвна разделяют на строительные и пиловочные.
Вид | Древесина | Предназначение |
Строительные | Сосна, лиственница, кедр; ель и дуб – реже; | Для несущих строительных конструкций: свай, элементов свайных опор, пролётных строений мостов, гидротехнических сооружений, опор воздушных линий связи. |
Пиловочные | Хвойные и лиственные; в фанерном производстве преимущественно – берёза, ольха, осина. | Бревно D = больше 200 мм являются сырьём для лущения в производстве фанеры и спичек. |
Пиломатериалы изготавливают путём продольной распиловки пиловочных брёвен. Виды лесных материалов можно увидеть на рисунке 6.
Рис.6
Материал | Размеры | Виды |
Доски | Толщина – 100 или менее мм; Ширина – в 3 раза или более превышает толщину. | Бывают: обрезные – с пропиленными кромками; необрезные – кромки не пропилены; |
Бруски | Толщина – менее 100 мм; Ширина – меньше трёхкратной толщины. | Разделяют: · Четырёхкантные (опиленные с 4-х сторон) · Двухкантные (опиленные с 2-х противоположных сторон по параллельным плоскостям) |
Брусья | Толщина и ширина выше 100 мм | |
Хвойные породы изготавливают длиной 1 -6,5 м с градацией через 0,25 м; Разделяют на 5 сортов. Лиственные породы – длиной 0,5 – 6,5 м с градацией через 0,5 м; Разделяют на 3 сорта. | ||
Шпалы (сосна, ель, лиственница, кедр, пихта, бук) | Длина – 2,5 – 2,7 м (для широкой колеи) и 1,35 – 1,8 м (для узкой колеи) | Изготавливают путём обработки круглого леса на 2 или 4 канта. |
Деревянные детали и сборные конструкции заводского изготовления поступают на строительство в готовом виде, а на строительной площадке производится лишь их сборка. В число деталей и сборных конструкций входят: балки междуэтажных и чердачных перекрытий, щиты для наката перекрытий и перегородок, элементы сборных деревянных домов.
Строганные или шпунтовые доски и бруски имеют на одной кромке шпунт, а на другой – гребень для плотного соединения элементов.
Фрезерованные изделия: плинтусы и галтели применяют для заделки углов между стенами и полом; поручни и наличники для обшивки оконных и дверных коробок.
Паркет бывает планочный и щитовой. Паркетные планки изготавливают из твёрдых пород – дуба, бука, ясеня и др. Щитовой паркет имеет основание из досок или брусьев, на которые наклеен паркет, набранный из отдельных планок. Паркетные доски состоят из реечного основания (которое позволяет избежать коробления), на которые наклеены паркетные планки. На кромках паркетных досок имеется паз для плотного соединения при настиле пола. Применение паркетных досок даёт большие преимущества по сравнению со штучным паркетом. Их изготовляют заводским механизированным способом, устройство чистого пола из паркетных досок производится значительно быстрее.
Столярные изделия – оконные и дверные коробки с вмонтированными в них оконными переплётами и дверными полотнами. Эти изделия изготавливают заводским путём и выпускают полностью отделанными.
Деревянная клееная конструкция (клееный профилированный брус) – монолитная совокупность деревянных деталей определённых параметров и взаиморасположения, соединённых клеевой прослойкой, предназначенная для выполнения несущих, ограждающих и/или эстетических (декоративных) функций в строительных конструкциях, а также в изделиях различного назначения (окна, двери, полы, мебель). Клееные деревянные конструкции и изделия отличаются меньшей массой, большой прочностью, водостойкостью, меньшей возгораемостью, чем обычные деревянные конструкции. Они почти не подвержены усушке и короблению. Изготавливаются в виде балок, ферм, арок. Склеиванием древесных заготовок из маломерного по длине и сечению пиленого материала можно изготовить дверные полотна, оконные и дверные коробки, щиты для полов, а также крупные конструктивные элементы (Рис.7).
Рис.7
Изготовление клееного бруса:
1. Специально отобранные брёвна (сосна, ель, лиственница) распускаются на доски.
2. Производится выборка досок
3. Отобранные доски просушиваются до относительной влажности 8 2 % и строгаются.
4. Производится вырезка дефектов: сучков, смоляных кармашек, гнили и т.д.
5. Отдельные доски по длине сращиваются на мини-шип – получается ламель, составная часть клееного бруса.
6. Производится строгание ламелей с 4-х сторон для получения точной геометрии перед склейкой.
7. Ламели склеиваются на мощном гидравлическом прессе в брус.
8. Брус профилируется.
Склеиваемых ламелей может быть от 2 до 5, что дает возможность изготавливать клееный брус достаточно "толстым" (максимальная толщина достигает 200 мм). Для склеивания ламелей между собой используют специальный высокопрочный водостойкий экологически чистый клей, который не препятствует возможности древесины "дышать". Особенность производства клееного бруса заключается также в том, что при склеивании в единый брус направление древесных волокон в ламелях задается в противоположные друг от друга стороны. Это позволяет достичь большей прочности клееного бруса по сравнению с цельным, а также избежать появления внутреннего напряжения и деформации конструкции при изменении влажности. С целью защиты древесного материала от воздействия ультрафиолета, влаги и быстрого возгорания клееный брус дополнительно обрабатывается специальными экологически чистыми составами.
Примеры клееных изделий:
Рис.8 – профили клееного бревна и бруса
Рис.9 – оконный профиль
Рис.10 – Мини-шип
Рис.8
Рис. 9 Рис.10
Фанера изготавливается из тонких слоёв древесины, так называемого шпона, срезаемого со ствола и очищенного от коры. Толщина шпона от 0,05 до 8 мм. Тонкий спиленный или срезанный шпон используется при изготовлении мебели или для декоративной отделки различных поверхностей.
Изготовление фанеры:
1. Шпон снимается с вращающихся брёвен при помощи специального станка в виде непрерывной ленты и наматывается на ролы, после чего его режут. Для изготовления шпона годится любая древесина предварительно размягчённая варкой или окуриванием для облегчения резки.
2. На нарезанный шпон специальной машиной наносится клей, затем шпон прессуется 5 – 25 минут при температуре 90 – 120 .
Рис. 11 – Шпон
Рис. 12 – Снятие шпона с бревна
t Jky23dpjaT1LPDFTvVr8y5cZdRARlsc7SN2SgI044FJ243zVpbzlLmT2I3Qzs6ZZmDtxS9iNn2Gn f9NOYpH8RlvlEL8aSSm5meCdeP2qP1Y6fuVWd9G+bbqQcfmiLLrf348tsmNkI2CWRznDyLZ9XVl+ 5fht8k+gv07y68jzC9tZs9zOPEXubTOuXV0/p92H9xdp2tY47fZ3vu9Da1rWhrQA0CgAwAAXRwZQ CAQCAQCAQCAQCAQCAQCAQCAQCAwQGCwRwr0o1nBBnBGBaDBAYIMYLGsrWBAIBAIBAIBAIBAIBAIB AIBAIBAIP//ZUEsBAi0AFAAGAAgAAAAhAIoVP5gMAQAAFQIAABMAAAAAAAAAAAAAAAAAAAAAAFtD b250ZW50X1R5cGVzXS54bWxQSwECLQAUAAYACAAAACEAOP0h/9YAAACUAQAACwAAAAAAAAAAAAAA AAA9AQAAX3JlbHMvLnJlbHNQSwECLQAUAAYACAAAACEACwJle1wCAACzBAAADgAAAAAAAAAAAAAA AAA8AgAAZHJzL2Uyb0RvYy54bWxQSwECLQAUAAYACAAAACEAWGCzG7oAAAAiAQAAGQAAAAAAAAAA AAAAAADEBAAAZHJzL19yZWxzL2Uyb0RvYy54bWwucmVsc1BLAQItABQABgAIAAAAIQCNFjPK3AAA AAUBAAAPAAAAAAAAAAAAAAAAALUFAABkcnMvZG93bnJldi54bWxQSwECLQAKAAAAAAAAACEAURnw zvQiAAD0IgAAFQAAAAAAAAAAAAAAAAC+BgAAZHJzL21lZGlhL2ltYWdlMS5qcGVnUEsFBgAAAAAG AAYAfQEAAOUpAAAAAA== ">
Рис.11
Рис.12
Стружечные плиты состоят из стружек необработанного дерева и древоподобных волокнистых материалов (стебли сахарного тростника и др.), которые смешиваются с отверждающими смолами и прессуются.
Изготовление:
1. Куски круглого дерева очищаются от коры и измельчаются специальными машинами, превращаясь в стружку или щепу различных размеров.
2. Полученный материал подвергается сушке и сортировке.
Два способа производства СП позволяют разделить их по расположению стружки на 2 вида:
· При плоском прессовании стружки, покрытые смолой, разбрасываются по заготовке так, что располагаются почти параллельно плоскости плиты. Иная структура плиты достигается разбрасыванием различной стружки. Затем заготовки прессуются при определённой температуре.
· При изготовлении плит на экструдерах стружка вместе со связующим выдавливается в литьевой канал и скорость экструзии рассчитана так, чтобы обеспечить одновременно с прессованием склеивание стружечного материала. Этим способом изготавливаются плиты в которых имеются продольные трубчатые отверстия.
Многопустотные плиты имеют высокие тепло- и звукоизоляционные показатели, поэтому широко используются в стеновых элементах.
Рис.13 – Стружечная плита
Древоволокнистые плиты. При их изготовлении древесина измельчается до волокон или пучков волокон, которые затем смешиваются со связующим и другими наполнителями, и из этой массы формируется новый материал. В полученном материале структура древесины уже неразличима.
Изготовление:
В качестве сырья может служить древесина хвойных пород низкого качества. Лиственные породы можно подмешивать в качестве добавки, так же как и другие добавки сено, хлопок, кокосовое волокно.
1. Сырьё рубят на мелкие кусочки, потом под воздействием водяного пара оно разбухает.
2. Затем его размельчают на мелкие волоконца с помощью дисковых мельниц.
· При мокром способе размельчённые волокна смешивают с водой, и они перемешиваются в мешалках в однородную массу. Большое количество воды, содержащиеся в массе, отделяется на сите под действием тяжести массы. Затем путём вакуумирования и отжатием на вальцах.
· Сухой способ заключается в том, что вместо воды используется воздух.
Древоволокнистые плиты используют в качестве теплоизоляционного материала для пола, стен, крыши.
Рис. 14 – ДВП
Сэндвич - панель состоит из 2 специальных стружечных плит, сделанных из ориентированной спрессованной плоской щепы в три слоя (ОСП), которые располагаются параллельно друг другу, между этими плитами под давлением помещается плита твёрдого пенополистирола — специального вещества, которое обладает пористой структурой, упругостью, а главное отсутствие запаха, также является абсолютно негорючим. Полученная сэндвич-панель наделена высочайшей прочностью, и максимальной стойкостью к любым погодным условиям, также она обеспечивает практически полную звукоизоляцию.
Еще одним очень важным свойством данного материала является то, что сэндвич - панель абсолютно экологична, как в процессе работы, так и в процессе эксплуатации, она совершенно не экстрагирует никаких опасных веществ и не имеет ограничений в сроках использования. сэндвич-панели, долголетние и выносливые, никогда не начнут разлагаться, в них не появятся трещины, а микроорганизмы, бактерии, плесень, насекомые и грызуны в них никогда не заведутся.
В результате проведенных исследований, было выяснено, что панель, которая имеет толщину всего 17 сантиметров, по своим теплозвукоизоляционным функциям равна:
· пятидесяти сантиметровой деревянной стене из бруса,
· двухметровой кирпичной стенке,
· четырехметровой бетонной стене.
Рис.15 – Сэндвич-панель
Похожие статьи:
poznayka.org
Древесина – материал будущего. Cтатьи. Наука и техника
Владимир ФРАДКИН
Разрабатывая новые строительные и конструкционные материалы, химики и технологи главное внимание уделяют их эксплуатационным свойствам. Такие критерии как экологичность или расход сырьевых и энергоресурсов отходят поначалу на второй план. Но, в конечном счете, они играют весьма заметную роль потому, что в значительной мере диктуют рыночную цену нового материала. Именно поэтому интерес к традиционным материалам на основе возобновляемых видов сырья стремительно растёт. Типичным примером может служить древесина. Благодаря новым технологиям она может сегодня во многих областях успешно конкурировать с металлами, полимерами и даже керамикой.
Древесина высокой плотности
Многие поколения строителей видели один из главных недостатков древесины в ограниченной возможности её формования. Специалисты Дрезденского технического университета разработали и запатентовали новую технологию обработки деревянных конструкций, которая существенно расширяет сферу их применения. При внешнем осмотре отличить обычный еловый брус от такого же бруса, но обработанного по дрезденскому методу, практически невозможно. Лишь взяв их в руки, замечаешь, что один почти вдвое тяжелее другого. Причина становится ясна при взгляде на торцы: на одном годовые кольца круглые, на другом – овальные, как бы сплюснутые. «Эта древесина подверглась уплотнению, – поясняет Пеер Халлер (Peer Haller), профессор Института строительных конструкций и деревянных сооружений при Дрезденском техническом университете. – Процесс уплотнения осуществляется при температуре 150°C прессом горячего прессования. При этом происходит сжатие микроструктуры древесины, и в результате мы получаем древесину очень высокой плотности – примерно 1 кг/дм3».
Один килограмм на кубический дециметр – это плотность воды. Сухая еловая древесина имеет в нормальном состоянии вдвое меньшую плотность – ведь она представляет собой своего рода губку. Именно высокая пористость древесины и позволяет из стволов круглого сечения получать методом горячего прессования без каких-либо потерь балки прямоугольного сечения.
Преимущества уплотнённой древесины
Преимущества уплотнённой древесины наиболее отчётливо проявляются при возведении крупных инженерных сооружений – например, мостов. Здесь нагрузки всегда распределяются крайне неравномерно, так что отдельные балки подвержены повышенному износу. Если эти балки изготовить из уплотнённой древесины, а все прочие того же сечения – из обычной, то такое решение позволит сохранить архитектурную гармоничность моста и при этом обеспечить оптимальные эксплуатационные характеристики.
Там, где ожидаемые нагрузки особенно велики, инженеры используют, как правило, стальные балки различного профиля. Широкое распространение получили, например, тавровое и двутавровое сечения. Однако и пустотелые балки коробчатого или круглого сечения способны нести большую нагрузку, чем сплошные массивные балки. Технология, разработанная профессором Халлером, позволяет получать пустотелые балки из древесины. Для этого сначала круглый ствол прессуется в брус квадратного сечения, а затем с одной стороны деформация снимается.
В результате квадратное сечение превращается в трапецеидальное, а это позволяет из нескольких таких балок сложить пустотелую трубу.
Как соединить древесину с полимером
Судя по всему, балки из уплотнённой древесины уже в скором времени появятся на многих стройплощадках. Древесина безусловно могла бы найти широкое применение и в машиностроительных отраслях, если бы не те трудности, с которыми до сих пор сталкиваются технологи при попытках прочно соединить деревянную основу с полимерным покрытием. Для этих целей сегодня используется клей, что далеко не всегда даёт оптимальные результаты. Теперь же специалисты Лазерного центра в Ганновере предложили другой метод – естественно, с использованием лазера. Штефан Барчиковски (Stefan Bartcikowsky) – один из разработчиков новой технологии – говорит:
– Нужно представлять себе дело так, что пластмасса для лазерного луча прозрачна. Лазерный луч как бы смотрит сквозь пластмассу, не замечая её, но видит за ней древесину. И вот там-то, на этой границе, и концентрируется энергия лазера. Древесина нагревается и подплавляет пластмассу, так что в результате образуется прочное сварное соединение, имеющее существенные преимущества перед клееным.
Одно из главных достоинств лазерной технологии – её гибкость: переналадить такую установку, приспособив её для решения новых задач, можно за считанные часы. Энергия лазерного луча должен быть подобрана с таким расчётом, чтобы температура в пограничном слое не превышала 400-т градусов, иначе древесина начинает обугливаться. Однако столь высокие температуры и не нужны, поскольку большинство полимеров плавятся уже при 90 градусах. Расплав затекает в поры древесины, благодаря чему и образуется прочное соединение. Штефан Барчиковски говорит:
– Сейчас ситуация такова: при испытании наших образцов на разрыв, то есть когда мы пытаемся снова отделить пластмассу от древесины, образец всегда рвётся не в зоне соединения, а в толще материала. Для нас это очень хороший признак: значит, полученное нами сварное соединение прочнее, чем сами соединяемые материалы.
Сегодня опытная установка ганноверских инженеров обеспечивает довольно скромную скорость сварки – 1 м/мин. Авторы разработки намерены значительно повысить мощность лазера, которая пока составляет всего 100 Вт, и довести скорость сварки до 80 м/мин. Учёные надеются, что уже через год смогут представить действующий прототип промышленной установки.
Древесина при производстве керамики
Между тем, древесину начинают применять при производстве керамики. До сих пор исходным материалом для неё служили минеральные порошки – например, тонко молотый карбид кремния помещался в форму и спекался. Но измельчение и спекание – весьма энергоёмкие процессы, а потому американские инженеры разработали более экологичную технологию производства керамики: она не только требует меньше энергии, но и использует в качестве исходного материала возобновляемое сырьё – древесину. Мритианджей Сингх (Mrityunjay Singh), научный сотрудник отдела НАСА по разработке новых керамических материалов в Кливленде, штат Огайо, говорит:
– Мы можем использовать даже опилки, утилизация которых является для лесопильных предприятий серьёзной проблемой. К опилкам добавляются вяжущие вещества, затем полученной массе придаётся форма будущей детали, после чего эта заготовка подвергается пиролизу.
Упомянутый Сингхом пиролиз – это не что иное, как разложение под действием высоких температур в бескислородной среде. Именно этот процесс позволяет превращать древесину в древесный уголь, который – с химической точки зрения – представляет собой чистый углерод. А затем в печь добавляется кремний – второй компонент будущей карборундовой керамики.
Кроме соединений кремния, могут быть использованы и расплавы некоторых солей, что позволяет производить широкий ассортимент современных керамик. Особенность предложенной технологии состоит в том, что на протяжении всего процесса сохраняется микроструктура древесины (иллюстрации срезов древесины см. в статье «Архитектура деревьев»), и керамика как бы перенимает некоторые свойства исходного материала. Для керамики с такими свойствами найдётся немало новых сфер применения.
От фильтрации воды до термозащиты космических аппаратов
В частности, – полагает Сингх, – она может быть использована для фильтрации питьевой воды. Учёные университета в Эрлангене испытывают керамические материалы на основе сосновой древесины в качестве катализаторов для химической промышленности. А НАСА полагает, что новый класс материалов как нельзя лучше подходит для термозащиты космических аппаратов.
По мнению Сингха, первые изделия из керамики на основе древесины могут появиться на рынке уже через год-два. Но каков промышленный потенциал этого нового класса материалов – пока неясно.
Ранее опубликовано:
Фрадкин В. Древесина: материал будущего. Немецкая волна. Знания и техника. 2003.
Смотри также:
Ковалев Ю. Архитектура деревьев. НиТ, 2003.
Дата публикации:
17 августа 2003 года
n-t.ru
Современные древесные материалы
С каждым новым днем современный мир растет, а значит, развивается и строительная отрасль, где на сегодняшний день возникает огромное множество отделки различного рода сырья при его изготовлении. При помощи современных методов готовая строительная продукция обладает весьма значительным процентом высокого уровня качества. При помощи, которых, увеличивается в разы, эксплуатация изделий, сокращая дополнительные расходы, денежных средств у домовладельцев и тем самым создавая качественные и надежные конструкции объектов.
Клееный деревянный брус
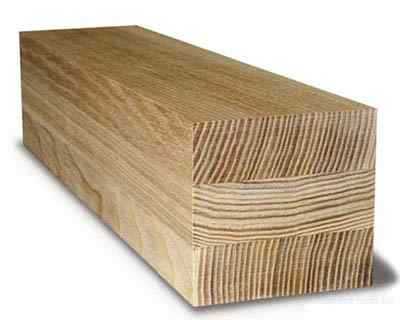
Древесный брус – является стволом дерева, которое, проходит специальную обработку, где обрезаются четыре стороны (Клееный брус), создавая прямоугольную форму, либо при использовании специального оборудования можно создать другую форму изделия. Как правило, брус больше всего предназначен для строительства домов, пристроек и много других строительных элементов. После окончательной обработки бруса, он получает весьма достойный внешний вид древесины, сохраняя длительно свою форму и, как правило, не теряет своих характеристик по теплоизоляции. Как выше было описано брус может обладать не только прямоугольной формой, а также и профилированной которая, задается в оборудовании при его обработке. При строительстве определенного объекта, как правило, строители особо уделяют внимание на то, чтобы конструкция носила в себе максимальную характеристику устойчивости к воздействию влаги, что бы предотвратить в дальнейшей эксплуатации ее размокание. Самыми главными достоинствами профилированного бруса являются то, что он не требует производства повторного утепления, так как во время эксплуатации, было замечено, что конструкция, данных свойств не теряет довольно длительное время. Также является весьма привлекательная цена для домовладельцев, решившим построить определенную конструкцию, так как за разумную цену предлагается построить качественную и долговечную постройку. Обрезная доска
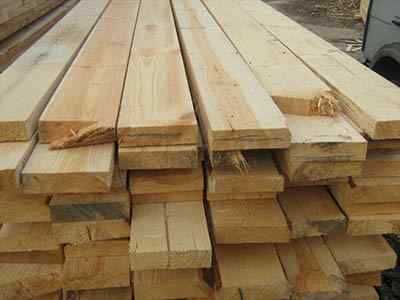
www.stroim-2014.ru
Шпон (древесный материал) - это... Что такое Шпон (древесный материал)?
Шпон (нем. Span, Spon ‒ щепка, подкладка), древесный материал в виде тонких листов древесины, получаемый лущением коротких брёвен (чураков) на лущильных станках (лущёный Ш.), строганием брусков на шпонострогальных станках (строганый Ш.), пилением на фанеропильных станках или горизонтальных лесопильных рамах (пилёный Ш.).Пилёный Ш. (толщина 1‒10 мм), вырабатываемый из древесины ели, кавказской пихты и сибирского кедра, отличается наиболее высоким качеством и используется для изготовления дек струнных музыкальных инструментов. Производство пилёного Ш. связано с большими потерями древесины на опилки (полезный выход Ш. из сырья не превышает 40%). Лущёный Ш. (0,1‒ 10 мм) вырабатывают из древесины берёзы, бука, дуба, ели, ольхи, осины, сосны и др. пород; это наиболее массовая разновидность Ш., широко используемая для изготовления фанеры, фанерных плит, древеснослоистых пластиков и др. видов слоистой клеёной древесины, для фанерования деталей и узлов столярных изделий, в спичечном производстве (спички, спичечные коробки), для изготовления сепараторов свинцовых электрических аккумуляторов и пр. Строганый Ш. (0,2‒5 мм) вырабатывают из древесины акации, бука, дуба, ильма, каштана, ореха, тисса, ясеня, карельской берёзы, красного дерева и др. ценных пород, обладающих красивой текстурой древесины. Декоративный эффект текстуры, получаемый на разных разрезах древесины, определяет выбор направления строгания при изготовлении Ш.; различают радиальный, радиально-тангентальный, тангентальный и тангентально-торцовый строганый Ш. Для обеспечения подбора Ш. по цвету и текстуре последовательно состроганные с одного бруса листы укладывают и упаковывают в пачки (кноли) в порядке строгания. Строганый Ш. применяют для фанерования столярных изделий.
Возрастающая дефицитность ценных пород древесины и трудность искусств. воспроизведения их текстуры, равноценной по декоративному эффекту натуральной древесине, делают особенно перспективными развитие производства тонкого и ультратонкого (0,08‒0,15 мм) Ш. ценных пород и облагораживание природной текстуры древесины рядовых пород спец. видами обработки (наклонное к продольной оси ствола строгание, волнистое строгание и лущение, коническое лущение и др.).
Лит.: Справочник фанерщика, 3 изд., М., 1968; Производство лущёного и строганого шпона, М., 1970; Канашкин И. А., Производство тонкого лущёного шпона, М., 1974.
И. К. Черкасов.
Большая советская энциклопедия. — М.: Советская энциклопедия. 1969—1978.
dic.academic.ru
Что такое древесина?
Давайте отгадаем загадку: что это может быть – материал, который имеет волокна, достаточно твердый и прочный? Основную его часть скрывает кора? Правильно! Это древесина. Для чего же нам нужна древесина? Разберемся по порядку.
Древесина состоит из большого количества трубковидных клеток, которые имеют оболочки преимущественно из целлюлозы. Пектаты кальция и магния сумели сцементировать все это в почти однородную массу. Используется древесина в качестве строительного материала, топлива. Наиболее часто применяют ее в качестве сырья для изготовления бумаги, искусственного волокна либо древесноволокнистых плит (для этого древесину предварительно измельчают и химически обрабатывают). Этот материал является одним из факторов развития цивилизации, без которого не представляют своего существования большинство промышленных отраслей.
Несмотря на то, что папоротники также имеют древесную ткань, люди получают древесину преимущественно из двух отделов царства высших растений – покрытосеменных и голосеменных. Голосеменные растения – это древняя форма древесных видов, которую представляют хвойные деревья (так называемые «мягкие породы» — сосна, кедр, ель). Покрытосеменные растения делятся на два класса – однодольные и двудольные. Древесную ткань имеют лишь некоторые из однодольных растений – пальмы, бамбук, юкка. Древесину двудольных растений, к которым относятся «твердые» породы – эвкалипт, дуб, клен преимущественно используют для мебели, отделки интерьеров и прочего.
Создание сайтов, которые специализируются на древесине, позволили нам узнать, что многократно делящиеся клетки прокамбия и камбия порождают клетки древесины. Камбий появляется из клеток, которые отделяются от конуса нарастания стебля либо корня. Корень начинает свое существование еще в клеточно-образовательном центре зародыша в семени. Для древесины являются характерными так называемые «Годичные кольца». Появляются они вследствие изменения размеров клеток, толщины их стенок (в зависимости от условий роста). Там где климат относится к умеренному – контраст колец отличается от «летней» древесины одного года и от «весенней» древесины следующего года. Согласно кольцам можно высчитать, сколько лет тому или иному дереву.
Древесина состоит из ряда достаточно сложных органических соединений. Если провести полный химический анализ, мы обнаружим, что древесина на 50% состоит из углерода, на 6% из водорода, и на 44% из кислорода. В составе древесины мы найдем от 45 % до 60% целлюлозы, примерно 15% — 35% лигнина, и от 15% до 25% гемицеллюлоза. В зависимости от породы будет варьироваться и количество экстрактивных инородных веществ. Оно может быть неодинаковым в ядровой древесине и заболони.
Создание интернет магазина позволит производителю и поставщику выгодно продать древесину, а покупателям найти своего поставщика этого материала.
ПОХОЖИЕ СТАТЬИ:
www.technologywood.ru