Простое приспособление для заточки сверл своими руками. Как сделать станок для заточки сверл своими руками
Станок для заточки сверл своими руками
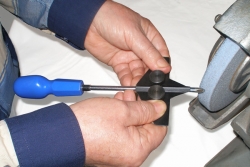
Пожалуй, каждый профессиональный мастер использует сверла для своей работы, которые должны быть качественными и отлаженными. Раньше сверла затачивались вручную, но сейчас большим успехом пользуются специальные станки для заточки сверл. Конструкция такого станка является очень простой. Для его создания вам потребуются простые материалы, которые присутствуют практически в каждом доме. Давайте вместе рассмотрим поэтапную схему изготовления точильного станка для сверл.
Содержание:
- Особенности заточки сверл
- Особенности точильных станков
- Станок для заточки сверл своими руками
- Процедура заточки сверл на станке
Особенности заточки сверл
Тупым сверлом практически невозможно сверлить поверхности. Острое сверло решит ситуацию в считанные минуты. Поэтому сверла должны быть заточенными под нужным углом и готовы к работе. Углы заточки для разных материалов не могут быть одинаковыми. Чем тверже материал, тем тупее будет угол. Например, для пластмассы подойдет угол заточки в 30-60 градусов, а для каленой стали в 130-140 градусов. Если к качеству сверления не предъявляется больших требований, можно выбрать угол заточки в 90-100 градусов.
Стоит отметить, что заточка сверл может производиться вручную на абразивных дисках или на затачивальных станках. Во время ручной заточки сверло необходимо держать за рабочую часть левой рукой и направлять его ближе к режущей части. Правая рука должна держаться за хвостовик. Прижмите режущую кромку сверла к боковой поверхности заточного абразивного круга. После этого необходимо повернуть сверло осторожным движением правой руки. При этом режущие кромки должны принять к оси правильный наклон и необходимую форму.
Затачивайте сверло сначала с одной стороны, а затем с другой. При этом очень важно контролировать заточку режущей кромки, чтобы острие находилось по центру. В противном случае при сверлении сверло будет уходить в сторону. Также не следует сильно давить на сверло, поскольку это может удлинить процесс заточки. Ручная заточка является не очень удобным способом, поскольку может повлечь за собой некоторые дефекты. К примеру, если режущие кромки после заточки сверла по длине не равны и наклонены под разными углами к оси сверла, середина поперечной кромки от оси сверла сместится, поэтому будет вращаться при работе вокруг оси. Поэтому лучше для этой цели использовать точильный станок для заточки сверл.
Во время заточки следует обратить внимание на изначально заданный угол. Именно на него следует ориентироваться. После этого посмотрите, в каком состоянии находится инструмент. Если повреждения являются серьезными, можно воспользоваться более грубым наждаком. Если же они незначительные, вам вполне хватит мелкозернистого наждачного диска. Для слабого затупления и совсем незначительных повреждений подойдет доводочный круг. Заточку сверла необходимо производить последовательно - сначала обработайте его верхнюю часть, аккуратно прижимая его к плоскости точильного круга.
После обработки задней поверхности, у вас должен получиться правильный конус, если смотреть сбоку. После этого обрабатывается режущая часть сверла, а затем окончательная доводка. Размер перемычки при правильной обработке сверла не должен быть больше 0,4 миллиметра для сверл, которые имеют диаметр от 8 миллиметров и менее. Если сверло имеет более крупные размеры, размер перемычки должен быть 1 - 1,5 миллиметра. Если вы никогда не затачивали сверла, мы рекомендуем вам потренироваться на других предметах. Так вы сможете быстрее понять технологию заточки и набить руку.
Особенности точильных станков
Станок для заточки сверл задействуется для затачивания сквозных и глухих сверл из стали, чугуна и твердых сплавов. Это оборудование может быть наделено разными функциями с учетом типа заточки, ее размеров и т.д. При работе со станком угол можно менять от 90 до 140 градусов. Станки могут быть бытовыми и промышленными. Бытовые станки для заточки сверл являются довольно компактными и больше подходят для домашнего использования. Они смогут затачивать сверла небольшого диаметра.
Промышленные станки наделены большей мощностью и рассчитаны на заточку сверл, которые имеют большой диаметр. Мощность определяется мотором прибора. Точильный станок для сверл обладает зажимом для сверла и заточным кругом, который рассчитан на использование более 2000 инструментов. Конструкция обеспечивает точную установку сверл, чтобы оператор мог контролировать процесс заточки. Станок работает от электросети. Как правило, точильные станки для сверл являются долговечными и простыми в использовании.
Стоит отметить, что бывают универсально-заточные станки и специализированные. Первый вариант может использоваться для разнообразных режущих инструментов, например для метчиков, фрезов, долбняков и зенкеров. Специализированные станки могут обрабатывать всего один вид инструмента, поэтому работают более точно. Именно к таким станкам и относится точильный станок для сверл. Причем для каждого варианта заточки сверл необходим свой станок.
Существует семь методов для затачивания сверл: одноплоскостной, фасонный, сложно-винтовой, эллиптический, винтовой, двухплоскостной и конический. На универсальных станках можно применять фасонную, одноплоскостную, эллиптическую и двухплоскостную заточку. Что касается остальных методов, для этого нужен специализированный электрический станок для заточки сверл. Если сверло имеет диаметр более 3 миллиметров, необходимо использовать станок с оптическим устройством. Если сверло имеет диаметр менее 1 миллиметра, необходимо применить бинокулярный микроскоп. Чтобы затачивать монолитные сверла, следует использовать алмазный круг.
Станок для заточки сверл своими руками
К сожалению, рынок товаров не всегда может предложить нам то, что действительно нужно, или цена станков для заточки сверл слишком высокая. В этом случае можно сделать станок самостоятельно. Если у вас имеется небольшой опыт по работе с техникой, вы очень легко справитесь с этим заданием.
Для этого вам понадобится тумблер, точильный круг, заглушка, мощный мотор, подставка, немного проводов и ось. Для соблюдения режима безопасности станок рекомендуется поместить в корпус, а снаружи оставить только ось с точильным кругом, которая немного выступает. Прибор будет работать от сети. Причем можно подключать его к источнику и пользоваться как легким и переносным станком.
Заранее побеспокойтесь о том, где будет стоять ваш станок для заточки сверл. Рекомендуется поместить его на металлический стол. Для этого необходимо поставить электродвигатель на столешницу, воспользовавшись креплениями, а затем отметить места отверстий для болтов. После этого следует убрать электродвигатель и просверлить четыре отверстия. Затем установите электродвигатель обратно и закрепите его, воспользовавшись болтами.
Электродвигатель самодельного станка для заточки сверл наделен валом, на который вам необходимо надеть зернистый диск. Если диаметр вала подходит диаметру отверстия в диске, необходимо надеть на вал шайбу, диск, затем снова шайбу. После этого ставится крепежная гайка, а резьба предварительно нарезается на валу. Можно использовать специальную насадку на круг, в которой сверло не качается и затачивается как карандаш. Вы можете ее сделать самостоятельно или приобрести в магазине.
Если диаметр вала является меньшим, нежели диаметр отверстия в камне, следует добавить втулку. В ней делается специальное отверстие и отверстие для болта, чтобы иметь возможность закрепить ее на валу. Тогда она не будет поворачиваться вместе с абразивным диском при работе. На конце втулки необходимо нарезать правую резьбу по ходу вращения диска, чтобы зафиксировать его, воспользовавшись шайбами и гайками. После этого втулка надевается на вал.
Если вам трудно определится с выбором электродвигателя, можно использовать вариант от старой стиральной машинки. Эта мощь будет наиболее оптимальной для заточки необходимых инструментов. Заранее приготовьте пускатель и отрезки проводов. Можно использовать провода от старой аппаратуры. Вы, конечно, можете приобрести и новые отрезки, но дешевле использовать подручные инструменты, которые есть в каждом доме. Поэтому если старые провода находятся в хорошем состоянии, их спокойно можно использовать.
Провод необходимо подсоединить к пускателю. Важно, чтобы пускатель имел минимум три нормально разомкнутых контакта (HP). Его обмотка должна подключаться к фазной линии через две кнопки, соединенные последовательно. Одна с h4, которая будет кнопкой выключения, а вторая с HP - кнопкой включения. Эта кнопка должна стоять в одной параллели с парой HP контактов пускателя.
Если нажать на кнопку включения, на обмотку подастся напряжение и контуры пускателя замкнутся, одна пара которых будет шунтировать кнопку. Если ее отпустить, напряжение не снимется с пускателя. Если нажать на кнопку выключения, мы разорвем цепь питания обмотки, а пускатель отпустит контакты, поэтому двигатель остановится.
Электродвигатель является безопасным даже при открытом виде, ему не нужна дополнительная защита, но рекомендуется сделать металлический короб, чтобы защитить конструкцию как минимум от пыли. Можно сделать стеклянный защитный экран. Это убережет ваши дыхательные пути и глаза от попадания пыли из круга. Рекомендуется установить защитный кожух, который должен закрывать торец абразивного диска на две трети. Его можно изготовить из старой камеры от авто. В случае раскола точильного диска, его части будут находиться в кожухе и не смогут причинить вред.
Процедура заточки сверл на станке
Большинство людей делают точильные станки для сверл своими руками. Чтобы не тратить лишние деньги, вы легко можете соорудить точильный станок для сверл самостоятельно. Причем вы можете сделать его универсальным и при необходимости затачивать на нем любые предметы. При работе нужно строго следовать инструкции к станку для заточки сверл и придерживаться определенных правил.
Наконечник сверла состоит из двух небольших плечиков. Крайне важно, чтобы они были одинаковыми. Не нужно сравнивать их высокоточными измерительными приборами, достаточно прикинуть на глаз. Но одинаковость должна быть обязательно. Место, где сходятся плечики, называется центром выполненного отверстия, радиус которого определяется длиной большего плечика. Если они будут одинаковыми, тогда ось вращения сверла совпадет с центром отверстия.
Если это не так, диаметр получится больше необходимого, причем на величину разницы между центральной точкой кривого отверстия и осью сверла. Это тот случай, когда сверло разбивает отверстие. Помимо этого, идет большая нагрузка на инструмент и руки, которая часто влечет за собой поломку сверла. Когда будете затачивать сверло, помните, что оно должно резать материал.
При изготовлении каждое изделие затачивается идеально, что очень сложно повторить в домашних условиях. Различные марки победита отличаются по методике получения сплава и химической формуле. Такие нюансы нельзя определить на глаз, поэтому название материала, которое подходит сверлу, должно писаться на упаковке. Внимательно изучите сторону вращения сверла, чтобы понять, какую сторону нужно затачивать.
Для настольного станка вам могут понадобиться заточные круги. Их еще называют наждаками, точилом или абразивным кругом. Всегда начинайте точить более грубым абразивом. Когда на инструменте появиться заусенец по всей длине, вы можете перейти на более мелкий абразив. Подбирайте бруски таким образом, чтобы каждый следующий мог убирать небольшие дефекты предыдущего. В заключение вы делаете окончательную доводку при помощи самого мелкого бруска с элементом полировки.
Всегда выдерживайте поставленный угол заточки. Но для этого вам следует немного попрактиковаться. Очень часто лезвие инструмента уезжает в сторону и перемещается. Точильный диск должен вращаться только по направлению от лезвия. Если же это будет наоборот, существует риск неправильной заточки и получения серьезных телесных повреждений.
Учтите, что сверла не выносят перегрева. Дело в том, что в процессе заточки твердосплавные пластины иногда трескаются и отваливаются. Но этого можно избежать. Постарайтесь не допустить чрезмерного нагревания сверла о точильный камень. Регулярно охлаждайте сверло водой. Но если сверло уже раскалилось докрасна, не макайте его в жидкость! Из-за этого пластины могут мгновенно растрескаться. Пусть изделие немного остынет самостоятельно.
Все спиральные сверла имеют по две режущие кромки и задние плоскости, которые делают окончание сверла коническим. Но если вы возьмете шайбу с меньшим диаметром в сравнении со сверлом и вмонтируете его в отверстие шайбы, то сможете увидеть, что режущие кромки сверла касаются шайб. При этом задняя часть поверхности отстает от режущих кромок.
При заточке сверл на станке своими руками обращайте внимание на соблюдение правил техники безопасности. Помните, что работа связана с острыми лезвиями, которые могут легко нанести травму. Мы надеемся, что наша простая инструкция поможет вам понять технологию заточки и соорудить качественный прибор собственными руками. Желаем вам успехов!
strport.ru
Приспособление для заточки сверл и приспособления к нему + Видео
Приспособление для заточки сверл – крайне полезная вещь в вашем доме. Не секрет, что тупым сверлом невозможно работать с твердыми поверхностями.
Особенности работы со сверлом
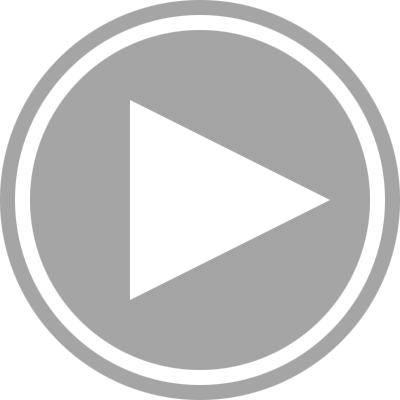
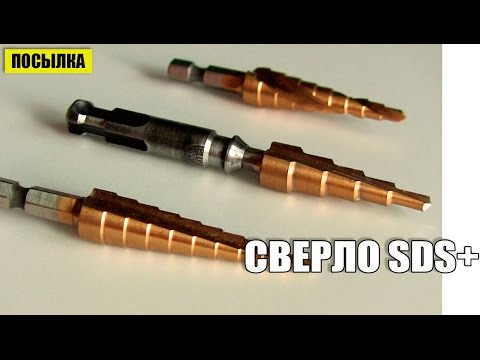
Видео про ступенчатые сверла
Заточка бурава может производиться вручную, на станках или специальных абразивных дисках.
Если вы затачиваете сверло вручную, то его необходимо:
- крепко держать за хвостовик, а другой рукой направлять его спиральную часть;
- режущую кромку сверла прижать к боковой поверхности абразивного круга;
- после заточки одной стороны необходимо плавно повернуть сверло, при этом режущие кромки обязательно должны иметь правильный наклон к оси и принять нужную конфигурацию.
Сверло затачивают с обеих сторон поочередно. При этом обязательно контролируйте режущие кромки.
Помните! Острие бурава должно находиться ровно по центру.
В противном случае при работе он будет отклоняться. Стоит отметить, что на сверло ни в коем случае нельзя сильно давить, иначе оно может получить дефекты (изгиб).
Например, если после заточки вы заметили, что режущие кромки неодинаковы и наклонены под разными углами к оси, то это значит, что середина поперечной кромки находится не в центре сверла, и оно будет неправильно работать.
Поэтому все специалисты рекомендуют использовать специальный заточной станок для сверл.
Во время заточки обязательно обратите внимание на изначальный угол инструмента. Именно он в дальнейшем станет вашим ориентиром. Затем осмотрите буравчик на предмет повреждений:
- если вы обнаружили серьезные дефекты, то можно воспользоваться грубой наждачной бумагой;
- если дефекты маленькие и сверло затуплено совсем чуть-чуть – воспользуйтесь доводочным кругом. Эта операция необходима для тонких буравов;
- если сверло по бетону имеет дефекты конуса хвостовика – обработайте верхнюю часть инструмента, аккуратно прижимая его к точильному кругу;
- после обработки ещё раз тщательно осмотрите заднюю поверхность бура;
- если вы заметили, или определили шаблоном, что у вас получился идеальный конус – вы правильно заточили инструмент.
После этого обработайте режущую кромку сверла. Размер перемычки при рациональном обтачивании инструмента должен быть 1-1,7 мм.
Какие особенности у точильных станков
Самодельное устройство для затачивания сверл рассчитано на сквозные и глухие буравчики из сталей, чугунок и различных твердых сплавов. В зависимости от типа, станки могут быть наделены разными функциями. На некоторых из них во время работы можно варьировать угол.
Станки для заточки бывают:
- универсальные – применяются для различных режущих инструментов;
- специализированные – для одного вида.
Именно к универсальным станкам относят устройства для заточки сверл, ведь на них можно обрабатывать:
- метчики;
- фрезы;
- долбняки;
- зенкеры.
Станки подразделяют на две категории:
- Промышленные – имеют высокую мощность и рассчитаны на заточку инструмента большого диаметра. Мощность зависит напрямую от двигателя.
- Бытовой точильный станок для сверл – достаточно компактный и используется зачастую для домашнего пользования. С его помощью можно обрабатывать даже буры малых диаметров.
Различают семь методов заточки:
- Одноплоскостной.
- Сложно-винтовой.
- Фасонный.
- Эллиптический.
- Конический.
- Двухплоскостной.
- Винтовой.
Как изготовить приспособление для заточки сверл
Для изготовления самодельного станка вам потребуются:
- тумблер;
- абразивный круг;
- заглушка;
- двигатель;
- подставка;
- провода.
Следуйте нашим советам:
- В целях безопасности поместите самодельный станок в корпус, снаружи оставьте только ось и абразивный круг. Помните, прибор будет работать от сети.
- Заранее выберите место, где будет стоять ваше приспособление для заточки сверл. Желательно, чтобы оно находилось на металлическом столе.
- Далее поставьте электродвигатель на столешницу с помощью креплений (струбцин) и отметьте места отверстий для болтов, если у него есть лапки.
- После этого уберите электромотор и сделайте 4 отверстия.
- Позже снова установите двигатель и аккуратно закрепите его с помощью болтов.
Совет: Если у двигателя нет лапок – можно укрепить его с помощью металлических полос (хомутов).
Электродвигатель для нашего будущего станка должен быть оснащен специальным удлиненным валом, на который следует надеть зернистый диск. Для этого:
- Установите крепежную гайку, предварительно нарезав на конце вала правую резьбу.
- Закрепите диск с помощью шайбы и гаек.
Если диаметр вала и отверстия диска совпадают, то установите на вал шайбу, а затем абразивный диск. Если диаметр вала и отверстия не совпадают, то вам необходимо добавить втулку.
Предварительно сделайте в ней специальное боковое отверстие с резьбой для болта, чтобы иметь возможность плотно закрепить её на вал. После этого вы можете надеть втулку.
Если вы не можете определиться с электродвигателем, то просто возьмите мотор старой стиральной машинки. Он идеально подойдет для самодельного устройства заточки.
Стоит отметить, что вы должны заранее приготовить пускатель и провода, которые впоследствии нужно будет соединить. Очень важно, чтобы пускатель имел как минимум три-четыре разомкнутых контакта. Его обмотка должна подключаться с помощью двух кнопок к фазной линии.
Внимание! Электродвигатель будет небезопасным, независимо от типа – при работе вращающийся вал может случайно намотать шнур, провод, волосы.
Совет: Изготовьте металлический короб для защиты станка от пыли, абразивных частиц, а вас – от случайных травм.
Как правильно заточить сверло на станке
- При заточке необходимо следить за тем, чтобы два плечика сверла были одинаковые. Если вы достигнете такого соответствия – значит ось вращения сверла полностью совпадет с центром отверстия.
- Перед началом заточки обязательно убедитесь в том, что абразивный диск плотно закреплен.
- Всегда начинайте процесс более грубым абразивом. После того, как на вашем сверле появится заусенец, вы можете сменить абразив на более мелкий.
- Следите за углом заточки.
- Не допускайте переключением обмоток, чтобы абразивный диск крутился наоборот. Он должен всегда двигаться только в направлении лезвия.
Учтите, что сверла не выносят излишнего перегрева. Во время заточки регулярно охлаждайте буравчик. Но ни в коем случае не опускайте в воду раскаленное докрасна сверло, так как в нем могут появиться каверны.
Дополнительные приспособления
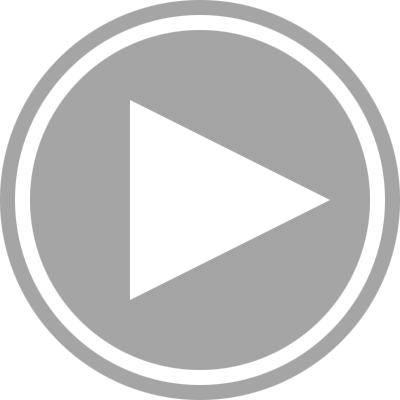
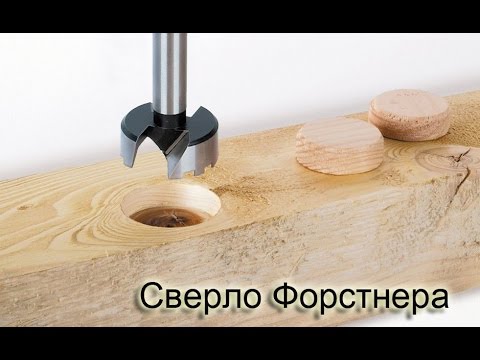
Видео про сверло Форстнера
- Направляющая
Чтобы не держать сверло в процессе заточки на весу (это может привести к травме) предусмотрите подложку или направляющую в виде маленькой приставки. Она выполняется из полосы металла, изгибается, как показано на рисунке и прикручивается к станине (основанию). Сверло опирают на нее и подводят к кругу под нужным углом.
- Угломер
Сделайте на направляющей, описанной выше, риски (отметки) под необходимые углы заточки. Пользоваться ей станет намного удобнее.
Если это для вас сложно – отрежьте верхнюю часть обычного транспортира и приклейте на направляющую.
Углы менее 300 для заточки не применяются, поэтому жертвуем ими.
- Универсальное приспособление
Для облегчения заточки инструмента, в частности сверл, разработан механизм, состоящий из сверлильного патрона, вала, роликовых направляющих (салазки) и транспортира.
Основную подложку, описанную выше, делают широкой. На нее приклеивают транспортир. Высверливают отверстие, в которое вставляют болт, служащий осью для поворотной поверхности.
На нее устанавливают на роликовых салазках пластину, на которой закреплена труба с патроном на оси. Сама пластина движется вперед/назад с помощью обычного механизма подачи (ось с резьбой).
В нижней части поворотной пластины укреплен указатель-ограничитель смещения. Он служит для поворота устройства на нужный угол и для его стопора.
Работа с приспособлением
- В патрон вставляется сверло.
- Пластину поворачивают на нужный угол и стопорят указателем.
- Крутят рукоять, добиваясь необходимой заточки половины сверла.
- Замечают деление.
- Поворачивают сверло на 900 и повторяют операцию, доводя сверло до замеченной точки.
refite.ru
Приспособление для заточки сверл с чертежом
Угол заточки сверл
Если говорить о тех сверлах, которые используются мастерами в домашних условиях, то стоимость их в магазинах невысока. Но даже в этом случае не стоит использовать их как расходный материал для одноразового применения. Ведь обновление сверла до самого хорошего рабочего состояния не составит большого труда, если мастер имеют сноровку или специальные приспособления.
Есть фабричные станочки, которые предназначаются для затачивания, но это отдельная статья расходов, поэтому чаще всего мастера создают такие устройства своими руками.
Больше всего проблем создают сверла по металлу, а деревянные заготовки не так скоро снижают остроту режущих кромок.
Чтобы изготовить станок для восстановления остроты режущих элементов, необходимые средства контроля (шаблон), который используется для поверки инструмента.
Обычно инструменты по черному металлу, твердосплавной бронзы, стали или чугуна — с углом кромки 115-125 градусов. Длина другого материала эти параметры иные.
для мягкой бронзы, красной меди – 125, для латунных сплавов – 135;
для алюминия и мягких алюминиевых сплавов, гранита, керамики и древесины – 135 градусов;
для магния и его сплавов – 85 градусов;
для пластика, текстолита и силумина – от 90 до 100 градусов.
Мастера при необходимости делают шаблоны соответственно указанным выше данным. Кстати, теоретически единичный экземпляр сверла может подойти для всех этих металлов и других материалов, если каждый раз точить разные рабочих поверхностей.
Элементарное кустарное приспособление, которое часто применяется, втулки, приделанные к основанию. В интернете много чертежей для самостоятельного изготовления. Нужно учесть, что инструмент должен быть хорошо зажат, точность зависит от 1 градуса.
При желании можно изготовить значительных размеров обойму, применив алюминиевые или медные трубки соотносительное с типовыми характеристиками сверл или в заготовке из мягкого металла просверлить много дырок. Необходимо, чтобы у точилки был комфортный подручник, чтобы перемещать устройство и удерживать упор.
Этот примитивный станок для заточки легко установить на верстак или столик.
Практический пример работы с чертежом
Суть проблемы: есть свёрла, их надо точить.Будем использовать один из методов заточки, близкий к заводским. Ловить руками лень. Лучше обезьяний способ — поставил и готово. На изготовление приспособления по готовому чертежу ушел приблизительно 1 час времени.
Немного сварочных работ по шаблону. Был сделан уголок. Надели шайбу, она просто напрессована.
Попробуем первые заточки, если всё собрано правильно, будем дорабатывать и окультуривать, делать приспособление на скорую руку.
После заточки сверла проводим тест. Видны две литьевые стружки, значит, заточка проведена правильно.
Единственный недостаток — одна стружка длиннее другой, значит промазали по длине кромок. Надо сделать упор, который станет регулировать длину заточки, обеспечит симметричность кромок. Для этого сделаем упорную шайбу, которая будет выставляться и протачиваться. Или подрежем, чтобы появилась возможность обрабатывать более короткие сверла.
Видео канала «Anton Fomenko».
izobreteniya.net
Как сделать приспособление для заточки сверл своими руками
Приспособление для заточки сверл своими руками изготовить достаточно просто, условиями успеха при этом будут знание правил выполнения заточки режущего инструмента, а также умение работать ручным инструментом и техническая смекалка.
Особенности заточки сверла
Основными правилами, обеспечивающим качественную заточку являются:
- за один проход необходимо снимать незначительный слой металла;
- в процессе выполнения работы выполняется неоднократное охлаждение сверла в водном или водно-содовом растворе;
- скорость вращения наждачного круга должна быть минимально возможной;
- сверло, во время заточки, не должно перегреваться;
- в процессе выполнения работы сверло направляется против движения абразивного круга.
Объем и характер выполняемой работы зависят от вида его износа режущего инструмента. Износ можно квалифицировать по:
- задней поверхности;
- перемычки;
- уголкам;
- фаске;
- передней поверхности.
В зависимости от вида заточки сверла, его технических характеристик, а также назначения, рекомендуются следующие виды их обработки, как-то:
Одинарная нормальная – «Н» | до 12,0 мм | Для универсального применения. Угол– в соответствии с обрабатываемым материалом. |
Одинарная с подточкой перемычки – «НП» | до 12,0 мм | Для обработки стального литья. Угол– 115-120°. |
Одинарная с подточкой перемычки и ленточки – «НПЛ» | свыше 12,0 мм | Для стали и стального литья, а также чугуна. Угол– 115-120°. |
Двойная с подточкой перемычки – «ДП» | свыше 12,0 мм | Для стали и чугуна с неснятой коркой. Заточка выполняется под двумя углами: 116-118° и 70-75°. |
Двойная с подточкой перемычки и ленточки – «ДПЛ» | свыше 12,0 мм | Для универсального использования. Угол– в соответствии с обрабатываемым материалом. |
По методу Жирова | свыше 12,0 мм | Используется при обработке хрупких материалов. Основной угол заточки – 118*, дополнительные – 70° и 55°. |
Как изготовить станок своими руками
Для заточки спиральных сверл может быть использован любой точильный станок (агрегат), работающий от электрической сети 380/220 Вольт, оснащенный наждачным кругом и оборудованный специальным приспособлением, обеспечивающим фиксацию затачиваемого сверла под определенным углом к оси вращения абразивного элемента устройства.
Основные требования к специальным приспособлениям, обеспечивающих качественное выполнение работ:
- Ось приспособления должна совпадать с осью вращения абразивного круга. Она может быть с ней в одной горизонтальной плоскости или быть несколько выше нее.
- Используемое оборудование и приспособления должны быть надежно закреплены.
- Конструкция приспособления должна давать возможность выполнять заточку сверла под различными углами, в зависимости от потребности пользователя.
Для изготовления одного из вариантов подобных устройств понадобится:
- Ручной слесарный инструмент, углошлифовальная машинка («болгарка»), сварочный аппарат.
- Листовая сталь толщиной 3,0 – 4,0 мм, а также стальная трубка небольшого диаметра, имеющаяся в наличии.

Работы по изготовлению станка выполняются в следующей последовательности:
- Используемый точильный станок (№5 на схеме) прочно закрепляется на выбранной поверхности.
- Из полосовой стали изготавливается площадка (№1 на схеме), на которой будет закрепляться сверло (№3 на схеме).
- Форма площадки может быть произвольной, единственное условие – в месте расположения сверла посредством «болгарки» делается канавка.
- На площадке просверливаются отверстия (№6 на схеме), служащие для закрепления крепежной пластины (№2 на схеме), а также отверстия, обеспечивающие соединение приспособления к точильному станку (на схеме не указаны).
- Форма и размер крепежной пластины могут быть произвольными.
- Из металлической трубки и полосовой стали изготавливается узел крепления к основанию точильного агрегата. Наличие трубки позволяет обеспечить перемещение приспособления в вертикальной плоскости – появляется возможность изменять угол заточки сверла.
- Узел крепления приспособления для заточки к корпусу точильного станка зависит от вида и устройства блока защиты наждачного круга (№4 на схеме), а также наличия упора (площадки) конкретного наждачного агрегата.
- При желании узел крепления может быть оборудован дополнительными элементами, обеспечивающими колебательное движение приспособления в горизонтальной плоскости, что позволит обеспечить требуемую артикуляцию в процессе выполнения работ.
- После того, как все элементы приспособления собраны, оно крепится к упору (кожуху) точильного станка и проверяется работоспособность изготовленного приспособления.
Несколько рекомендаций по выбору наждачных кругов

Для заточки винтовых сверл можно использовать различные наждачные круги, но в свете того, что данный расходный материал (инструмент) изготавливается из прочной стали, то и абразивные элементы должны этому соответствовать.
Основные требования к наждачным кругам:
- Марка электрокорунда – 24А, 25А, 91А и 92А.
- Зернистость – 25-40.
- Твердость — М3-СМ2
Приспособление для заточки сверл может быть выполнено и в ином, отличном от предложенного варианта исполнении — как более простой, так и сложной конструкции. Вид такого приспособления определяется его потребностью и умения пользователя изготавливать оснастку своими руками.
stroypomochnik.ru
Приспособление для заточки свёрл своими руками: доступные чертежи

Чтобы обработка материалов была качественной и быстрой, важно позаботиться о необходимой остроте сверла.
Регулярная замена используемого инструмента требует значительных финансовых затрат, а потому прекрасной альтернативой станет приспособление для заточки свёрл своими руками. Тем более что сделать его в домашних условиях не так уж сложно – достаточно подобрать подходящие чертежи и материалы.
Насколько актуально использовать оборудования для заточки
Как быстро сверло теряет свою остроту? Это зависит от множества различных факторов: обрабатываемого материала, скорости подачи, наличия дополнительного охлаждения, частоты оборотов. Если речь идет о работе с деревом, то заточка сверла требуется не так часто, как при обработке металла.
Пренебрегать этой процедурой бессмысленно – лучше потратить около получаса на то, чтобы вернуть инструменту былую остроту, чем напрасно терять время. Ведь продуктивность работы значительно снижается, приходится прикладывать дополнительные усилия, увеличивая нажим. Но в любом случае, процесс замедляется, а соответственно, на одну заготовку придется потратить в 2 раза больше времени.
Регулярная покупка новых сверл актуальна только в том случае, если речь идет о незначительных объемах работы. В противном случае, уровень затрат начинает расти в геометрической прогрессии – гораздо проще научиться их правильно затачивать на самодельном станке.
Выбор угла заточки
Как определить, что сверлу требуется замена? Как правило, мастер слышит неприятный скрипящий звук, а для обработки металла приходится прилагать дополнительные усилия. Изначально затупляется угол режущей кромки.
Если своевременно не принять необходимые меры, то срок эксплуатации инструмента на порядок сократится – процесс износа будет проходить активнее.
Важно учитывать, что в процессе заточки на станке необходимо подобрать правильный угол – он зависит от того, с какими материалами предстоит работать. В данном случае лучше всего руководствоваться довольно простым правилом: чем тверже обрабатываемая поверхность, тем тупее должен быть угол сверла.
Соответственно:
- Пластмасса – 30-60.
- Древесина – 40-60.
- Цветные металлы – 40-50.
- Каленая сталь – 130-140.
При желании можно воспользоваться и универсальным вариантом, заточив сверло под углом 90-100 градусов. Но это решение актуально только в том случае, если качеством обработки можно пренебречь.
Как сделать простейшую конструкцию?
В домашних условиях удобнее всего пользоваться станком для заточки, который легко сделать своими руками. Тем более что для этого потребуется лишь немного усилий и материалы, которые найдутся под рукой. Можно подобрать простейший чертеж – работа займет минимум времени.
Стойка для заточки состоит из основания, которое надежно зафиксировано и державки, рассчитанной на работу со сверлами разного размера, что делает подобное устройство поистине универсальным.
Для изготовления самодельного оборудования для заточки, потребуются следующие элементы:
- Основание – для этой цели потребуется подобрать доску, толщина которой составляет не менее 30 мм.
- Рейка – крепится к основанию любым удобным способом (можно как приклеить, так и прибить это изделие). Фиксируется под углом около 30 градусов. Боковая грань должна быть скошена. Этот элемент необходим для установки державки под нужным углом.
- Державка – для её создания потребуется брусок древесины прямоугольной формы. Одна грань должна быть скошена (примерно 60-65 градусов) – именно эта часть и крепится к рейке. С другой стороны нужно проделать отверстия различного размера для всех типов используемых сверл.
- Наждачный круг – используется для быстрой и качественной заточки. Также для этой цели можно приобрести алмазный круг – хоть стоимость и выше, но и срок его эксплуатации гораздо выше.
Простейший станок готов. Конструкция достаточно компактна по размеру, а потому для её установки не потребуется выделять дополнительное место – наверняка она успешно разместиться на одном из углов стола.
Оборудование с электродвигателем своими руками
При желании, можно создать и более совершенную конструкцию, пользоваться которой гораздо удобней, а на обработку тратиться минимум времени. Для этого потребуется подобрать подходящий мотор, а также позаботиться о выборе корпуса, что сделает работу приспособления безопасной.
Для изготовления подобного станка нужно лишь подобрать подходящий чертеж, а также придерживаться выбранного алгоритма действий:
- Установить двигатель на выбранную основу, либо же на стол (отличным решением станет электродвигатель от старой стиральной машины).
- Отметить места будущих креплений, сделать отверстия и закрепить мотор.
- Закрепить на валу двигателя зернистый круг (можно воспользоваться специальной насадкой на диск, которая сделает процесс заточки проще и быстрее).
- Если диаметр вала отличается от размеров абразивного диска, необходимо установить втулку.
- Соединить провода с пускателем – последний должен иметь минимум 3 разомкнутых контакта.
- Установить короб из металла — он необходим для защиты оборудования от пыли, что позволит увеличить срок эксплуатации двигателя.
В качестве дополнительной защиты можно использовать защитный кожух – он должен закрывать диск на 2/3. В этом случае, даже если в процессе выполнения работ круг расколется, мастер будет в безопасности.
Секреты правильной заточки
Чтобы обеспечить качественную заточку сверл, недостаточно подобрать подходящий чертеж и изготовить самодельный станок.
Важно еще и запомнить несколько простых правил, которые помогут без труда добиться желаемого результата:
- В процессе обработки поверхности инструмента, важно следить за тем, чтобы острие всегда располагалось по центру.
- Имеет смысл сначала потренироваться и только после этого приступать к работе – это поможет научиться выдерживать необходимый угол и не давить на изделие слишком сильно.
- Перегрев недопустим – можно просто-напросто испортить инструмент, а потому важно постоянно его охлаждать (если поверхность раскалилась, то нельзя опускать её в воду – сначала нужно дать изделию остыть).
- Начинать процесс рекомендуется с грубого абразива, после чего переходить к более мелкому.
И самое главное, всегда соблюдать технику безопасности – тогда и с процедурой заточки не возникнет ни малейших сложностей.
Процесс изготовления станка, используемого для быстрой и качественной заточки, довольно прост. Он не требует существенных затрат, так как для его создания прекрасно подойдут материалы, которые наверняка найдутся под рукой. При этом подобная стойка позволит сэкономить на частом обновлении инструмента, что весьма выгодно.
zonametalla.ru
видео, как сделать устройство своими руками, заточные приспособления
Сверла из металла есть практически в каждом хозяйстве, и когда они становятся тупыми, сделать с ними что-то практически невозможно. Именно поэтому их требуется периодически затачивать. Для этого есть специальные заточные станки для сверл, которые можно приобрести в магазине, но они не совсем дешевые, поэтому многие делают такие приспособления и своими руками.
Сегодня вы узнаете, как сделать станок для заточки сверл своими руками и даже посмотрите видео на эту тематику.
Точильные станки для сверл: классификация
Самодельный станок для заточки сверл подходит для того, чтобы точить такие виды инструментов:
- сверла на основе разных металлов;
- фреза;
- резаки;
- резцы;
- метчики;
- зенкера.
Точильное устройство бывает:
- универсальным – подходит для любого вида сверл или резаков;
- специализированным – предназначается для заточки только определенного типа инструментов.
Если говорить конкретно о самодельных устройствах, то они относятся к универсальным. А вот промышленные станки для заточки отличаются своей мощностью и предназначены для крупных инструментов из металла. В домашних условиях они не совсем практичны, поскольку они слишком габаритные, тратят много энергии и шумно работают.
А чтобы осуществлять заточку сверл из металла малого и среднего диаметра, подойдет и устройство, сделанное своими руками, отличающееся экономичностью и компактностью.
Что нужно для изготовления точильного станка своими руками
Чтобы своими руками собрать станок для заточки сверл, вам потребуются:
точильный диск;
- заглушка;
- электрический мотор;
- тумблер;
- подставка;
- кабель.
Алгоритм выполнения работы: видео
Ниже предлагаем посмотреть на видео особенности изготовления самодельного станка для заточки. Также вы прочтете, в каком порядке выполняются действия.
Все составляющие нужно разместить внутри корпуса, так будет удобнее работать. В доступности должен оставаться только шкив электродвигателя, на него надеваем точильный диск. Далее крепим к верстаку станок, место выбираем заранее. Алгоритм действий такой:
- устанавливаем в нужном месте электромотор и отмечаем на столе места креплений;
- сверлим отверстия для болтов;
- ставим электромотор на место и прикручиваем к верстаку с помощью хомутов из тонких полосок металла;
- ставим защитный корпус;
- на шкив двигателя ставим сам точильный круг.
Двигатель лучше всего выбирать с удлиненным шкивом. Первой наденьте шайбу, потом круг. Если поперечники шкива и диска не совпадают, то примените переходную втулку. Сбоку нее сделайте резьбовое отверстие и вкрутите в него крепежный болт.
В плане мощности двигателя для самодельного станка хорошо подойдет устройство от старой стиральной машины. А вот двигатель с большими оборотами не подойдет, поскольку заточка сверл осуществляется при небольшой скорости.
Далее подключите электрические приспособления – тумблер и двигатель, затем соединяем их с розеткой.
Дополнительные приспособления для станка
Станок для заточки сверл можно существенно усовершенствовать, если оснастить его дополнительными приспособлениями. Ниже рассмотрим их характеристики.
Так, шаблон для проверки можно сделать из листа тонкого металла диаметром в 1 мм. Для этого подойдет медь или алюминий. С помощью шаблона можно выявлять углы рядом с острием и между перемычками и рабочими краями, а также их продолжительность. Поскольку задний угол заточки сверла таким образом проверить вряд ли получится, можно выверить угол заострения. Шаблон вырезают перед первым применением сверла.
Также из полосок металла можно сделать маленькую приставку – направляющую, которую фиксируют на корпусе станка болтами. При работе станка сверло кладут на нее и подводят к точильному камню.
Угломер можно сделать посредством нанесения деления углов заточки на подставке. Можете отрезать немного металлического транспортира с угловыми отметками и прикрепить к подставке. Отрезать следует часть с углами от 30 градусов, поскольку при заточке более мелкие не применяются.
Значительно облегчить процесс заточки можно с помощью устройства, которое состоит из фиксированной станины и державки с отверстиями для вставки резаков разных размеров. При этом державка снимается. Станину делают из досок 50 мм, затем к ней крепят под углом в 32 градуса рейку, а она выставляет державку с инструментом под нужным углом.
Своими руками державку можно выпилить из бруска, его поверхность снимается под углом в 65 градусов, а скошенной частью кладут к рейке. В зависимости от типа заточки определяются и углы скашивания державки и рейки.
Также усовершенствовать работу станка по заточке сверл можно с помощью многофункционального механизма, который включает в себя такие элементы, как:
транспортир;
- роликовые салазки;
- сверлильный патрон;
- вал;
- направляющая.
Направляющая должна быть широкой, а к ней прикрепляют транспортир. Для оси поворота есть болт, который вставляют в отверстие. С поворотной части ставят подвижную пластину и направляющие. На пластине нужно зафиксировать трубку и ось, которая с одной стороны заканчивается сверлильным патроном, а со второй рукояткой. Упорная пластина перемещаться будет с помощью резьбовой оси.
Внизу упорной пластины расположен ограничитель, который указывает нужный угол смещения и фиксирует в требуемом положении.
Принцип работы заточного механизма такой:
- сверло в патроне фиксируем;
- под требуемым углом стопорим упорную пластину;
- рукояткой по продольной оси вращаем инструмент;
- отмечается угол;
- резак переворачивается на 90 градусов и может обработать вторую часть сверла до определенного угла.
Где и как поставить станок для заточки?
Чтобы заточка была удобной, станок нужно правильно установить. В этом есть ключевое правило – инструмент должен быть установлен горизонтально и с учетом исключения минимальной вибрации. Для этого можно предусмотреть специальный столик на ножках из металла. С этой целью можно использовать швеллер, трубу или крупный уголок. Вся столешница вместе со станком должна быть прочной. Именно поэтому листовое железо для подставки не подойдет.
Для подставки лучше всего брать толстое дерево и правильно прикрепить, чтобы обеспечивалась максимальная надежность крепления.
Если вы предусмотрели систему включения двигателя, обязательно уточните, можно ли будет изменять количество оборотов, поскольку, возможно, придется иметь дело с разными типами сверл. Помните, что чем тверже металл, тем ниже будет угловая скорость движения абразивного круга.
Как работать с самодельным станком
При заточке с помощью самодельного станка помните следующее:
два плечика во время работы должны быть одинаковыми, так сверло ровно пройдет в отверстие, и сверление будет выполняться правильно;
- до запуска станка хорошо закрепите на шкиве точильный круг;
- первая обработка проводится с помощью диска с крупным абразивом, при обнаружении на сверле заусенец, диски меняют на тонкие;
- при заточке все время держите нужный угол;
- круг должен двигаться только по лезвию в одном направлении;
- не перегревайте резак и во время обработки его иногда охлаждайте. Перегретый инструмент не окунайте в холодную воду, чтобы металл не повредился;
- сначала заточите одну сторону сверла, потом аккуратно переверните и обрабатывайте вторую.
При работе очень важно сохранить первоначальную форму инструмента и направление режущих краев. Внимательно следите за тем, чтобы не было смещения от центра острия кончика, поскольку инструмент при обработке может сильно отклониться. А если после заточки угол краев будет разным, сверло не сможет нормально работать. Это можно будет определить с помощью шаблона или же без него: смотрите, чтобы по форме кончик был конусообразным. Править лучше с помощью специальных устройств, чтобы не допустить ошибок.
Также очень важно правильно определить, когда сверло нуждается в заточке, многие это сделать не могут. Так, о затуплении сверла говорят такие явления:
- гудение или скрежет в начале сверления;
- металл нагревается быстро, иногда нагрев сопровождается сильным запахом.
Если заточить сверло раньше срока, то можно значительно сократить срок его эксплуатации и спровоцировать скорую поломку. Поэтому точильный станок нужно не только правильно собрать, но и правильно использовать только в соответствии с необходимостью.
Сохранить
instrument.guru
Zatochit sverlo. Как самостоятельно заточить сверло своими руками в домашних условиях вручную или с использованием специальных приспособлений. Как самому сделать станок для заточки сверл
Сегодня мы поговорим о том, как самостоятельно заточить сверло своими руками в домашних условиях вручную или с использованием специальных приспособлений. Так же рассмотрим технологию, позволяющую самому сделать станок для заточки сверлСкорость затупления сверла зависит в частности от оборотов, скорости подачи, охлаждения и других факторов, однако как ни старайся, время работы сверла до неудовлетворительной работоспособности измеряется минутами. Если объем работы значительный, постоянно покупать новые сверла получится накладно, поэтому лучше научиться их затачивать. Хотя все равно стоит иметь несколько сверл одного диаметра (3-10, в зависимости от ох диаметра и соответственно цены) чтобы возвращаться к заточке только когда затупились все сверла.
На периферии сверла скорость резания максимальна, и, следовательно, максимален нагрев режущих кромок. В то же время отвод тепла от уголка режущей кромки сильно затруднен. Поэтому затупление начинается с уголка, потом распространяется на всю режущую кромку. Ясно видно ее закругление. Затем истирается задняя грань. На ней появляются штрихи, риски, идущие от режущей кромки. По мере износа риски сливаются в сплошную полоску вдоль режущей кромки, более широкую у периферии и сужающуюся к центру сверла. Поперечная режущая кромка при износе сминается.В начале затупления сверло издает резкий скрипящий звук. Если сверло вовремя не заточить, количество выделяемого тепла будет возрастать и процесс износа пойдет быстрее.
Чтобы облегчить контроль геометрии сверла, главное, что следует сделать - это шаблон описанный ниже. С его помощью, даже если заточка выполняется без приспособлений, всегда можно проверить, где ещё нужно снять металл, и, в конце концов, получить то, что и должно получиться (не может быть чтобы не получилось, даже если придется сточить половину длинны сверла). Для соблюдения симметрии старайтесь, чтобы время заточки каждого участка и сила нажима были постоянные.
Тупым сверлом практически невозможно сверлить поверхности. Острое сверло решит ситуацию в считанные минуты. Поэтому сверла должны быть заточенными под нужным углом и готовы к работе. Углы заточки для разных материалов не могут быть одинаковыми. Чем тверже материал, тем тупее будет угол. Например, для пластмассы подойдет угол заточки в 30-60 градусов, а для каленой стали в 130-140 градусов. Если к качеству сверления не предъявляется больших требований, можно выбрать угол заточки в 90-100 градусов.
Стоит отметить, что заточка сверл может производиться вручную на абразивных дисках или на затачивальных станках. Во время ручной заточки сверло необходимо держать за рабочую часть левой рукой и направлять его ближе к режущей части. Правая рука должна держаться за хвостовик. Прижмите режущую кромку сверла к боковой поверхности заточного абразивного круга. После этого необходимо повернуть сверло осторожным движением правой руки. При этом режущие кромки должны принять к оси правильный наклон и необходимую форму.
Затачивайте сверло сначала с одной стороны, а затем с другой. При этом очень важно контролировать заточку режущей кромки, чтобы острие находилось по центру. В противном случае при сверлении сверло будет уходить в сторону. Также не следует сильно давить на сверло, поскольку это может удлинить процесс заточки. Ручная заточка является не очень удобным способом, поскольку может повлечь за собой некоторые дефекты. К примеру, если режущие кромки после заточки сверла по длине не равны и наклонены под разными углами к оси сверла, середина поперечной кромки от оси сверла сместится, поэтому будет вращаться при работе вокруг оси. Поэтому лучше для этой цели использовать точильный станок для заточки сверл.
Во время заточки следует обратить внимание на изначально заданный угол. Именно на него следует ориентироваться. После этого посмотрите, в каком состоянии находится инструмент. Если повреждения являются серьезными, можно воспользоваться более грубым наждаком. Если же они незначительные, вам вполне хватит мелкозернистого наждачного диска. Для слабого затупления и совсем незначительных повреждений подойдет доводочный круг. Заточку сверла необходимо производить последовательно - сначала обработайте его верхнюю часть, аккуратно прижимая его к плоскости точильного круга.
После обработки задней поверхности, у вас должен получиться правильный конус, если смотреть сбоку. После этого обрабатывается режущая часть сверла, а затем окончательная доводка. Размер перемычки при правильной обработке сверла не должен быть больше 0,4 миллиметра для сверл, которые имеют диаметр от 8 миллиметров и менее. Если сверло имеет более крупные размеры, размер перемычки должен быть 1 - 1,5 миллиметра. Если вы никогда не затачивали сверла, мы рекомендуем вам потренироваться на других предметах. Так вы сможете быстрее понять технологию заточки и набить руку.
Станок для заточки сверл задействуется для затачивания сквозных и глухих сверл из стали, чугуна и твердых сплавов. Это оборудование может быть наделено разными функциями с учетом типа заточки, ее размеров и т.д. При работе со станком угол можно менять от 90 до 140 градусов. Станки могут быть бытовыми и промышленными. Бытовые станки для заточки сверл являются довольно компактными и больше подходят для домашнего использования. Они смогут затачивать сверла небольшого диаметра.
Промышленные станки наделены большей мощностью и рассчитаны на заточку сверл, которые имеют большой диаметр. Мощность определяется мотором прибора. Точильный станок для сверл обладает зажимом для сверла и заточным кругом, который рассчитан на использование более 2000 инструментов. Конструкция обеспечивает точную установку сверл, чтобы оператор мог контролировать процесс заточки. Станок работает от электросети. Как правило, точильные станки для сверл являются долговечными и простыми в использовании.
Стоит отметить, что бывают универсально-заточные станки и специализированные. Первый вариант может использоваться для разнообразных режущих инструментов, например для метчиков, фрезов, долбняков и зенкеров. Специализированные станки могут обрабатывать всего один вид инструмента, поэтому работают более точно. Именно к таким станкам и относится точильный станок для сверл. Причем для каждого варианта заточки сверл необходим свой станок.
Существует семь методов для затачивания сверл: одноплоскостной, фасонный, сложно-винтовой, эллиптический, винтовой, двухплоскостной и конический. На универсальных станках можно применять фасонную, одноплоскостную, эллиптическую и двухплоскостную заточку. Что касается остальных методов, для этого нужен специализированный электрический станок для заточки сверл. Если сверло имеет диаметр более 3 миллиметров, необходимо использовать станок с оптическим устройством. Если сверло имеет диаметр менее 1 миллиметра, необходимо применить бинокулярный микроскоп. Чтобы затачивать монолитные сверла, следует использовать алмазный круг. Станок для заточки сверл своими руками
К сожалению, рынок товаров не всегда может предложить нам то, что действительно нужно, или цена станков для заточки сверл слишком высокая. В этом случае можно сделать станок самостоятельно. Если у вас имеется небольшой опыт по работе с техникой, вы очень легко справитесь с этим заданием.
Для этого вам понадобится тумблер, точильный круг, заглушка, мощный мотор, подставка, немного проводов и ось. Для соблюдения режима безопасности станок рекомендуется поместить в корпус, а снаружи оставить только ось с точильным кругом, которая немного выступает. Прибор будет работать от сети. Причем можно подключать его к источнику и пользоваться как легким и переносным станком.
Заранее побеспокойтесь о том, где будет стоять ваш станок для заточки сверл. Рекомендуется поместить его на металлический стол. Для этого необходимо поставить электродвигатель на столешницу, воспользовавшись креплениями, а затем отметить места отверстий для болтов. После этого следует убрать электродвигатель и просверлить четыре отверстия. Затем установите электродвигатель обратно и закрепите его, воспользовавшись болтами.
Электродвигатель самодельного станка для заточки сверл наделен валом, на который вам необходимо надеть зернистый диск. Если диаметр вала подходит диаметру отверстия в диске, необходимо надеть на вал шайбу, диск, затем снова шайбу. После этого ставится крепежная гайка, а резьба предварительно нарезается на валу. Можно использовать специальную насадку на круг, в которой сверло не качается и затачивается как карандаш. Вы можете ее сделать самостоятельно или приобрести в магазине.
Если диаметр вала является меньшим, нежели диаметр отверстия в камне, следует добавить втулку. В ней делается специальное отверстие и отверстие для болта, чтобы иметь возможность закрепить ее на валу. Тогда она не будет поворачиваться вместе с абразивным диском при работе. На конце втулки необходимо нарезать правую резьбу по ходу вращения диска, чтобы зафиксировать его, воспользовавшись шайбами и гайками. После этого втулка надевается на вал.
Если вам трудно определится с выбором электродвигателя, можно использовать вариант от старой стиральной машинки. Эта мощь будет наиболее оптимальной для заточки необходимых инструментов. Заранее приготовьте пускатель и отрезки проводов. Можно использовать провода от старой аппаратуры. Вы, конечно, можете приобрести и новые отрезки, но дешевле использовать подручные инструменты, которые есть в каждом доме. Поэтому если старые провода находятся в хорошем состоянии, их спокойно можно использовать.
Провод необходимо подсоединить к пускателю. Важно, чтобы пускатель имел минимум три нормально разомкнутых контакта (HP). Его обмотка должна подключаться к фазной линии через две кнопки, соединенные последовательно. Одна с h4, которая будет кнопкой выключения, а вторая с HP - кнопкой включения. Эта кнопка должна стоять в одной параллели с парой HP контактов пускателя. Если нажать на кнопку включения, на обмотку подастся напряжение и контуры пускателя замкнутся, одна пара которых будет шунтировать кнопку. Если ее отпустить, напряжение не снимется с пускателя. Если нажать на кнопку выключения, мы разорвем цепь питания обмотки, а пускатель отпустит контакты, поэтому двигатель остановится.
Электродвигатель является безопасным даже при открытом виде, ему не нужна дополнительная защита, но рекомендуется сделать металлический короб, чтобы защитить конструкцию как минимум от пыли. Можно сделать стеклянный защитный экран. Это убережет ваши дыхательные пути и глаза от попадания пыли из круга. Рекомендуется установить защитный кожух, который должен закрывать торец абразивного диска на две трети. Его можно изготовить из старой камеры от авто. В случае раскола точильного диска, его части будут находиться в кожухе и не смогут причинить вред.
Процедура заточки сверл на станкеБольшинство людей делают точильные станки для сверл своими руками. Чтобы не тратить лишние деньги, вы легко можете соорудить точильный станок для сверл самостоятельно. Причем вы можете сделать его универсальным и при необходимости затачивать на нем любые предметы. При работе нужно строго следовать инструкции к станку для заточки сверл и придерживаться определенных правил.
Наконечник сверла состоит из двух небольших плечиков. Крайне важно, чтобы они были одинаковыми. Не нужно сравнивать их высокоточными измерительными приборами, достаточно прикинуть на глаз. Но одинаковость должна быть обязательно. Место, где сходятся плечики, называется центром выполненного отверстия, радиус которого определяется длиной большего плечика. Если они будут одинаковыми, тогда ось вращения сверла совпадет с центром отверстия.
Если это не так, диаметр получится больше необходимого, причем на величину разницы между центральной точкой кривого отверстия и осью сверла. Это тот случай, когда сверло разбивает отверстие. Помимо этого, идет большая нагрузка на инструмент и руки, которая часто влечет за собой поломку сверла. Когда будете затачивать сверло, помните, что оно должно резать материал.
Перед началом работ убедитесь, что вращающийся шлифовальный диск надежно закреплен на верстаке. Рекомендуется одеть защитные очки. Качественная заточка требует минимум получаса. Проявите аккуратность и терпение - тогда инструмент заточится правильно и будет работать соответственно. Для правильной заточки сверла вы должны знать его тип - по металлу или по дереву.
При изготовлении каждое изделие затачивается идеально, что очень сложно повторить в домашних условиях. Различные марки победита отличаются по методике получения сплава и химической формуле. Такие нюансы нельзя определить на глаз, поэтому название материала, которое подходит сверлу, должно писаться на упаковке. Внимательно изучите сторону вращения сверла, чтобы понять, какую сторону нужно затачивать.
Для настольного станка вам могут понадобиться заточные круги. Их еще называют наждаками, точилом или абразивным кругом. Всегда начинайте точить более грубым абразивом. Когда на инструменте появиться заусенец по всей длине, вы можете перейти на более мелкий абразив. Подбирайте бруски таким образом, чтобы каждый следующий мог убирать небольшие дефекты предыдущего. В заключение вы делаете окончательную доводку при помощи самого мелкого бруска с элементом полировки.
Всегда выдерживайте поставленный угол заточки. Но для этого вам следует немного попрактиковаться. Очень часто лезвие инструмента уезжает в сторону и перемещается. Точильный диск должен вращаться только по направлению от лезвия. Если же это будет наоборот, существует риск неправильной заточки и получения серьезных телесных повреждений.
Учтите, что сверла не выносят перегрева. Дело в том, что в процессе заточки твердосплавные пластины иногда трескаются и отваливаются. Но этого можно избежать. Постарайтесь не допустить чрезмерного нагревания сверла о точильный камень. Регулярно охлаждайте сверло водой. Но если сверло уже раскалилось докрасна, не макайте его в жидкость! Из-за этого пластины могут мгновенно растрескаться. Пусть изделие немного остынет самостоятельно.
Все спиральные сверла имеют по две режущие кромки и задние плоскости, которые делают окончание сверла коническим. Но если вы возьмете шайбу с меньшим диаметром в сравнении со сверлом и вмонтируете его в отверстие шайбы, то сможете увидеть, что режущие кромки сверла касаются шайб. При этом задняя часть поверхности отстает от режущих кромок.
Заточку сверла производят по его задним граням. Очень важно, чтобы оба пера (зуба) сверла были заточены совершенно одинаково. Выполнить это вручную очень трудно. Не просто также вручную создать требуемую форму задней грани и заданный задний угол (где какой угол см. ниже).
Для заточки существуют специальные станки или приспособления. Если есть возможность, то лучше затачивать сверла на специализированном оборудовании. Но в условиях домашней мастерской такой возможности, как правило, не бывает. Сверла приходится затачивать вручную на обыкновенном точиле.
В зависимости от того, какую форму придают задней поверхности, существуют разные виды заточки: одноплоскостная, двухплоскостная, коническая, цилиндрическая, винтовая.
При одноплоскостной заточке заднюю поверхность пера выполняют в виде плоскости. Задний угол при такой заточке должен быть 28-30°. При одноплоскостной заточке велика опасность выкрашивания режущих кромок. Этот способ, самый легко выполнимый при ручной заточке, рекомендуют для сверл диаметром до 3 мм. Универсальные сверла диаметром больше 3 мм обычно подвергают конической заточке. Для того, чтобы были понятны особенности такой заточки, рассмотрим схему конической заточки на станке сверла с углом 2φ в 118°. На рисунке ниже показан шлифовальный круг и прижатое к его торцу режущей кромкой и задней поверхностью сверло.
Представим себе конус, образующая которого направлена вдоль режущей кромки и торца шлифовального круга, а вершина отстоит от диаметра сверла на 1,9 его величины. Угол при вершине равен 26°. Ось сверла пересекается с осью воображаемого конуса под углом 45°. Если вращать сверло, вокруг оси воображаемого конуса (как бы катать конус по торцу шлифовального круга), то на задней грани сверла образуется коническая поверхность. Если ось сверла и ось воображаемого конуса находятся в одной плоскости, то задний угол будет равен нулю. Чтобы образовался задний угол, нужно сместить ось сверла по отношению к оси воображаемого конуса. На практике это смещение будет равным 1/15 диаметра сверла. Качание сверла по оси воображаемого конуса при таком смешении обеспечит конусную заднюю грань и задний угол 12-14°. Чем больше величина смещения, тем большим будет задний угол. Следует напомнить, что задний угол вдоль режущей кромки меняется и увеличивается к центру сверла.
Понятно, что выполнить все эти условия заточки вручную очень сложно. Сверло, предназначенное к заточке, берут левой рукой за рабочую часть, возможно ближе к заборному конусу, а правой за хвостик.
Режущей кромкой и задней поверхностью сверло прижимают к торцу шлифовального круга и, начиная от режущей кромки, плавными движениями правой руки, не отрывая сверла от камня, покачивают его, создавая на задней грани пера конусную поверхность. Затем повторяют ту же процедуру для второго пера.
При заточке желательно как можно точнее повторить ту форму задней поверхности, которая была после заводской заточки, чтобы не потерять требуемые задние углы. Другой способ заточки, широко применяемый домашними мастерами, заключается в следующем. Как и в предыдущем случае, сверло берут левой рукой за рабочую часть возможно ближе к заборному конусу, а правой за хвостик. Режущей кромкой сверло прижимают к торцу шлифовального круга и плавным движением правой руки, не отрывая сверла от камня, поворачивают его вокруг своей оси, затачивая заднюю поверхность. Очень важно сохранить при вращении сверла нужный угол его наклона к торцу шлифовального круга. Для этого часто при заточке используют специальные втулки.
В результате такой заточки на задних поверхностях обоих перьев получится конусная поверхность, но не будет образован задний угол. При работе трение задней поверхности о стенки отверстия и, следовательно, нагрев будет больше.
Из-за трения о шлифовальный круг, при заточке происходит нагрев инструмента. Это вызывает отпуск закаленной части инструмента. Металл мягчеет, теряет твердость. Неумелое затачивание приводит лезвие инструмента в негодность. Поэтому заточку следует вести с многократным охлаждением сверла в воде или в водно-содовом растворе. Это требование не касается твердосплавных сверл. Нельзя при заточке пользоваться для охлаждения маслом. Если по каким бы то ни было обстоятельствам инструмент затачивают всухую, то: за один проход снимают незначительный слой металла; скорость вращения абразивного круга должна быть как можно ниже; сверло никогда не должно нагреваться до такой степени, чтобы этого не терпела рука.
Практика показывает, что заточку инструмента следует вести против движения шлифовального круга. Тогда режущая кромка более долговечна, реже ее сминание и обламывание.
Для заточки используют шлифовальные круги из электрокорунда (марок 24А, 25А, 91А, 92А) зернистостью 25-40, твердостью М3-СМ2, на керамических связках.
В производстве обычно за заточкой следует доводка. Доводка делает поверхность глаже, убирает мелкие зазубринки. Сверло, подвергнутое доводке, более стойко к износу, чем сверло после заточки. Если у вас есть возможность выполнить доводку, воспользуйтесь ею. Для доводки применяют шлифовальные круги из зеленого карбида кремния марки 63С зернистостью 5-6, твердостью М3-СМ1 на бакелитовой связке или круги из эльбора ЛО, зернистостью 6-8 на бакелитовой связке.
Одно из основных условий правильной заточки сверла - сохранение его осесимметричности. Обе режущие кромки должны быть прямолинейны и иметь идентичную длину, тождественную величину углов при вершине (и углы заострения) по отношению к оси сверла.
Правильность заточки проверяют специальным шаблоном.
Его делают самостоятельно из листа меди, алюминия или стали толщиной приблизительно 1 мм. Самый долговечный шаблон, конечно, из стали. Шаблоном проверяют угол при вершине, длину режущих кромок, угол между перемычкой и режущей кромкой. Вместо заднего угла, который весьма сложно измерить, шаблоном измеряют угол заострения. Шаблон целесообразно сделать перед началом использования нового сверла, чтобы с последнего перенести нужные углы.
Неравномерная длина режущих кромок и наклон их к оси сверла приводят и к неодинаковой нагрузке. Сверло быстрее выйдет из строя из-за интенсивного износа перегруженной режущей кромки.
Неравномерная нагрузка на части сверла вызовет его биение в процессе резания и, как результат, увеличение диаметра полученного отверстия.
Самый простой способ проверки правильности заточки - пробное сверление. Если перья сверла заточены неодинаково, то у менее нагруженного будет меньше стружки из соответствующей канавки. Иногда стружка выступает лишь через одну канавку. Диаметр отверстия может быть преувеличен в сравнении с диаметром сверла.
Приспособление для заточки сверла. Приспособление состоит из неподвижного основания и съемной державки с отверстиями для сверл разного диаметра.

На обычный подпятник (подлокотник) приспособление не установишь, так что придется придумывать для него какой-то столик или полку, можно перенести заточной станок на стол где будет место и для этого приспособления. На основание уложите вплотную к рейке державку с вставленным в нее сверлом, подлежащим заточке. Сверло в гнезде державки поверните так, чтобы затачиваемая кромка была сориентирована горизонтально. Левой рукой держите сверло у затачиваемой кромки, правой - хвостовик сверла. Прижимая державку к скошенной рейке, подведите сверло к наждачному кругу и заострите одну кромку. Затем разверните сверло и так же обработайте вторую кромку.
Можно сделать и проще: Углы заточки и другие характеристики сверла
Спиральное сверло представляет собой стержень, имеющий для облегчения выхода стружки две винтовые канавки. Благодаря канавкам на сверле образуются два винтовых пера, или, как их иначе называют, зуба.
Спиральное сверло состоит из рабочей части, шейки, хвостовика и лапки. Рабочая часть разделяется на режущую и направляющую. Все режущие элементы сверла расположены на режущей части - заборном конусе. Направляющая часть служит для направления во время резания и является запасной при переточке сверла. На перьях направляющей части по винтовой линии расположены цилиндрические фаски-ленточки. Ленточка служит для направления сверла в отверстии, а также для уменьшения трения сверла о стенки отверстия. Она не должна быть широкой. Так, ширина ленточки сверла диаметром 1,5 мм составляет 0,46 мм, диаметром 50 мм - 3,35 мм. Хвостовик сверла и лапка служат для закрепления сверла в шпинделе станка или патроне. Сверла могут быть выполнены как с шейкой, так и без нее.
Диаметр сверла, измеренный по ленточкам, неодинаков по длине сверла. У заборного конуса он несколько больше, чем у хвостовика. Это уменьшает трение ленточек о стенки отверстия.
Для того чтобы понять устройство режущей части сверла, рассмотрим основные принципы работы любого режущего инструмента (в том числе и сверла). Одно из важнейших требований к режущему инструменту состоит в том, чтобы отделяемая стружка свободно отходила от места резания. Поверхность инструмента, по которой сбегает стружка, называют передней гранью. Эту грань отклоняют назад под некоторым углом от вертикальной плоскости.
Благодаря этому углу для инструмента облегчено врезание в металл и стружка свободнее сходит по передней грани. Угол между передней гранью инструмента и плоскостью, проведенной перпендикулярно к поверхности резания, называется передним углом и обозначается греческой буковой γ.
Поверхность инструмента, обращенную к детали, называют задней гранью. Ее отклоняют на некоторый угол от поверхности обрабатываемой детали, чтобы уменьшить трение инструмента о поверхность резания. Угол между задней гранью инструмента и поверхностью резания называют задним углом и обозначают греческой буквой α.
Угол между передней и задней гранью инструмента называют углом заострения и обозначают греческой буквой β.
Угол между передней гранью инструмента и поверхностью резания называют углом резания и обозначают греческой буквой δ. Этот угол представляет собой сумму угла заострения β и заднего угла α.
Передний и задний угол - это те углы, которые необходимо соблюдать при заточке.
А теперь найдем описанные выше грани и углы на сверле, которое совсем не похоже на инструмент, изображенный на рисунке выше. Для этого рассечем режущую часть сверла плоскостью АБ, перпендикулярной его режущей кромке.
Режущая кромка - это линия пересечения передней и задней граней инструмента. Передний угол γ у сверла образует винтовая канавка. Угол наклона канавки к оси сверла определяет величину переднего угла. Величина углов γ и α вдоль режущей кромки переменна, о чем будет рассказано ниже.
Сверло имеет две режущие кромки, соединенные между собой перемычкой, расположенной под углом ψ к режущим кромкам.
Получив общее представление о геометрии режущей части сверла, поговорим подробнее о ее элементах. Передняя грань спирального сверла представляет собой сложную винтовую поверхность. Грань - это название условное, так как слово "грань" предполагает плоскость. Винтовая канавка, поверхность которой образует переднюю грань, пересекаясь с заборным конусом, создает прямые режущие кромки.
Угол наклона винтовой канавки к оси сверла обозначают греческой буквой ω. Чем больше этот угол, тем больше передний угол и тем легче выход стружки. Но сверло с увеличением наклона винтовой канавки ослабляется. Поэтому у сверл с малым диаметром, имеющих меньшую прочность, этот угол делают меньше, чем у сверл большого диаметра. Угол наклона винтовой канавки зависит также от материала сверла. Сверла из быстрорежущей стали могут работать в более напряженных условиях, чем сверла из углеродистой стали. Поэтому для них угол ω может быть больше.
На выбор угла наклона влияют свойства обрабатываемого материала. Чем он мягче, тем угол наклона может быть больше. Но это правило применимо в производстве. В домашних условиях, где одно сверло используют для обработки разных материалов, угол наклона обычно связан с диаметром сверла и изменяется от 19 до 28° для сверл диаметром от 0,25 до 10 мм.
Форма канавки должна создавать достаточное пространство для размещения стружки и обеспечивать легкий отвод ее из канавки, но при этом не очень ослаблять сверло. Ширина канавки должна быть приблизительно равна ширине пера. Глубина канавки определяет толщину сердцевины сверла. От толщины сердцевины зависит прочность. Если канавку сделать глубже, стружка будет лучше размещаться, но сверло будет ослаблено. Поэтому толщину сердцевины выбирают в зависимости от диаметра сверла. В сверлах малого диаметра толщина сердцевины составляет большую долю диаметра сверла, чем в сверлах большого диаметра. Так, для сверл диаметром 0,8-1 мм ширина сердцевины 0,21-0,22 мм, а для сверл диаметром 10 мм ширина сердцевины 1,5 мм. С целью повышения прочности сверла толщину сердцевины увеличивают по направлению к хвостовику.
Переднюю грань у сверла не перетачивают.
Конструкция винтовых канавок такова, что по мере приближения от края сверла к центру их угол наклона уменьшается, а значит, уменьшается и передний угол. Условия работы режущей кромки у центра сверла будут труднее.
Задний угол, так же как и передний, изменяется по величине в разных точках режущей кромки. В точках, расположенных ближе к наружной поверхности сверла, он меньше, в точках, расположенных ближе к центру, больше. Задний угол образуется при заточке заборного конуса и на периферии сверла равен приблизительно 8-12°, а в центре 20-25°.
Перемычка (поперечная кромка) расположена в центре сверла и соединяет обе режущие кромки. Угол наклона перемычки к режущим кромкам ψ может быть от 40 до 60°. У большинства сверл ψ=55°. Перемычка образуется пересечением двух задних граней. Ее длина зависит от толщины сердцевины сверла. Так как толщина сердцевины увеличивается по направлению к хвостовику, длина перемычки возрастает в результате каждой заточки. В процессе сверления поперечная кромка только мешает внедрению сверла в металл. Она не режет, а скребет или, вернее, давит металл. Недаром ее когда-то называли скребущим лезвием. С уменьшением длины перемычки вдвое усилие подачи можно снизить на 25%. Однако уменьшение длины перемычки за счет уменьшения толщины сердцевины приведет к ослаблению сверла. .
Большое влияние на работу сверла оказывает угол при вершине 2φ. Если угол при вершине мал, стружка своим нижнем краем будет задевать за стенку отверстия и условий для правильного образования стружки не будет.
Край стружки в этом случае хорошо укладывается в канавку. Изменение угла при вершине изменяет длину режущей кромки и, следовательно, нагрузку на единицу ее длины. При увеличении угла при вершине нагрузка на единицу длины режущей кромки растет, при этом увеличивается сопротивление внедрению сверла в металл в направлении подачи. При уменьшении угла при вершине возрастает усилие, необходимое для вращения сверла, так как ухудшаются условия образования стружки и возрастает трение. Но при этом нагрузка на единицу длины режущей кромки уменьшается, толщина срезаемой стружки становится меньше и теплота от режущих кромок отводится лучше.crovlya-krisha.blogspot.com