Нож из обоймы подшипника своими руками. Как сделать нож из подшипника
Как сделать нож из подшипника
Дело в том, что обойма подшипника круглая, а распрямить ее на полоску металла можно только с помощью ковки.
Для изготовления ножа своими руками можно использовать не только обойму подшипника, но и шарики или ролики из него.Подшипниковая сталь очень хорошего качества, ведь подшипники работают в очень жестких условиях и под большой нагрузкой, так что лезвие ножа откованного из подшипника получается с хорошими механическими свойствами. Такое лезвие хорошо держит заточку и не ломается.
Посмотрите видео - изготовление ножа из подшипника методом ковки.
Фактически такой нож из подшипника может выковать любой желающий, в ковке ножей нет никаких секретов.Особенности изготовления ножа из подшипника
1.Обойма подшипника распиливается болгаркой на заготовки необходимой длины.2. Ковка ведется при достаточно низкой температуре от светлокрасного до темнокрасного.
3. Обдирку делаем перед закалкой на точиле или ленте.
4. Желательно произвести нормализацию - разогрев до 750-770С, затем выдержка 5-7 мин и охлаждение на воздухе. Проводится 2-4 раза.
5. Закалка. Закалка самодельного ножа из подшипника производится при температуре 830С. Определять температуру можно по магниту - прикладываешь к заготовке и как перестало магнититься - пора закаливать.
Можно предварительно ориентироваться по поваренной соли - температура плавления соли 800 градусов. Посыпаем заготовку солью и калим, как соль на клинке начала плавиться, то берется магнит и проверяется достижение температуры закалки.
6. Закалка производится в масле. Температура масла 45-60 градусов. Выдержать в масле надо в течении часа, при этом нельзя болтать заготовку и прислонять ее к стенкам.
7. После закалки надфиль должен скользить по стали. А клинок - царапать стекло.
8. После закалки необходимо произвести отпуск, для этого самодельный нож из подшипника кладется в духовку на 2 часа и греется до температуры 160-200 градусов. Охлаждение производится простым отключением духовки.
Чем толще нож - тем меньше можно ставить температуру. Отпуск уменьшает хрупкость лезвия, но снижает закалку. Более толстый клинок выдерживает нагрузку на излом за счет своих габаритов, так что можно отпускать при меньшей температуре.
9. Заточка самодельного ножа из подшипника производится на алмазных брусках. а шлифовка ведется с помощью алмазной пасты.
Правильно изготовленный нож из подшипника царапает стекло, не тупится и не ломается при изгибающих нагрузках.
www.makeknife.ru
Нож из обоймы подшипника своими руками
Сегодня у нас мастер-класс по изготовлению ножа своими руками.
Всем привет! Сегодня мы будем делать нож из обоймы подшипника. Это будет вещь, которую приятно будет иметь при себе.
И так, берем наружную обойму от автомобильного подшипника, разрезаем его вдоль.Теперь нам нужно ее нагреть и разогнуть. В холодном виде это сделать не удастся.
Разогнутую заготовку нагреваю и расплескиваю молотком до плоского металла.
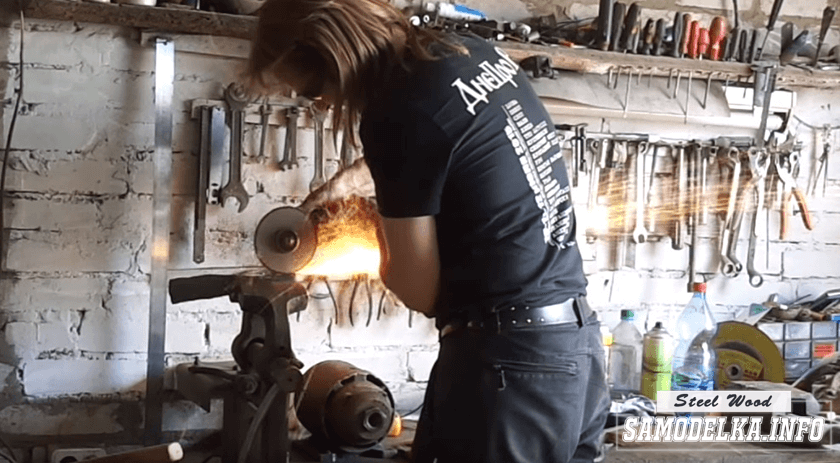
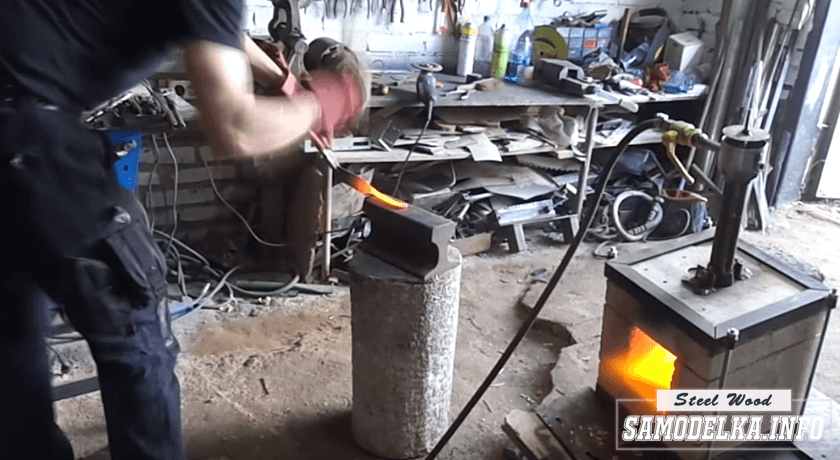



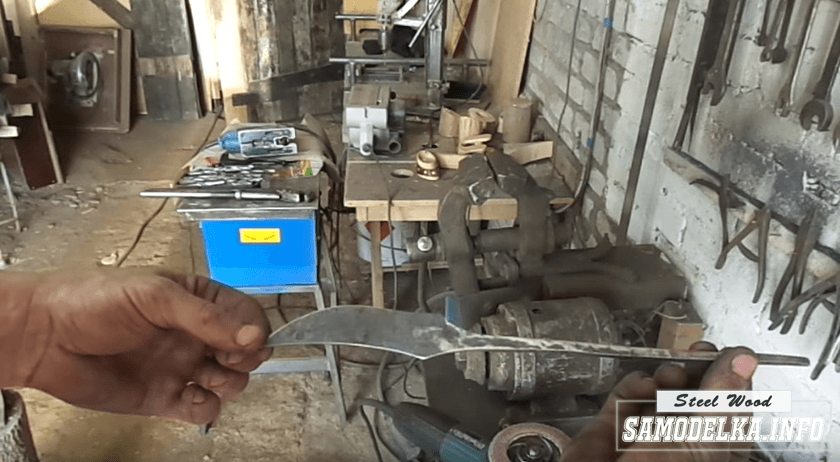
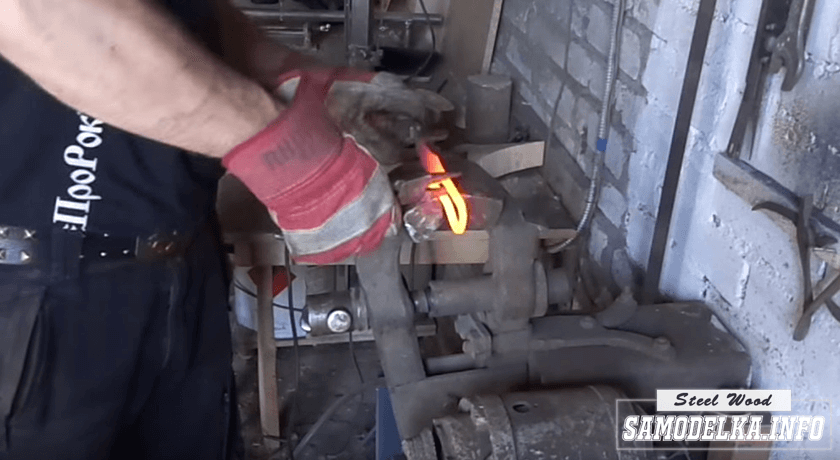
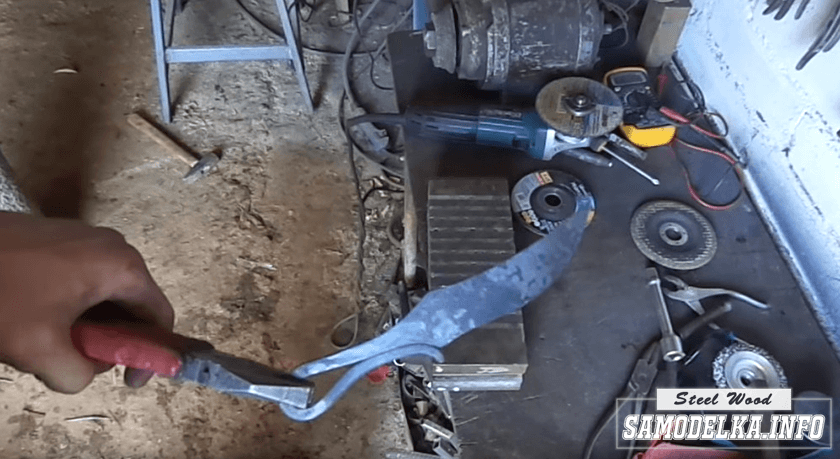
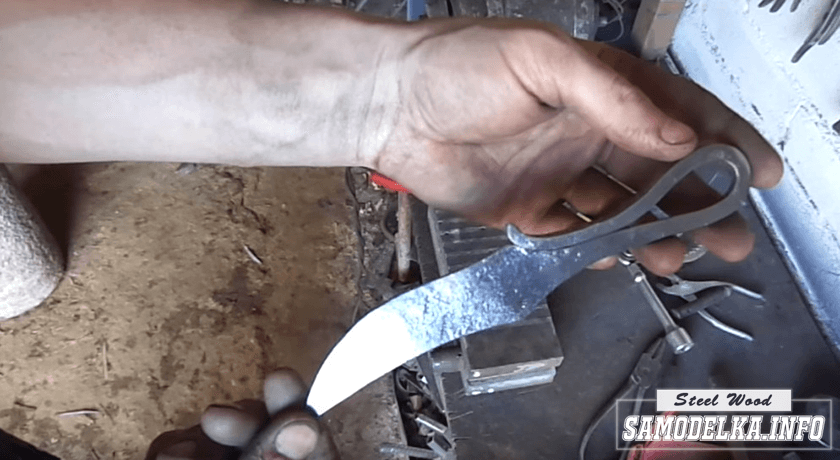
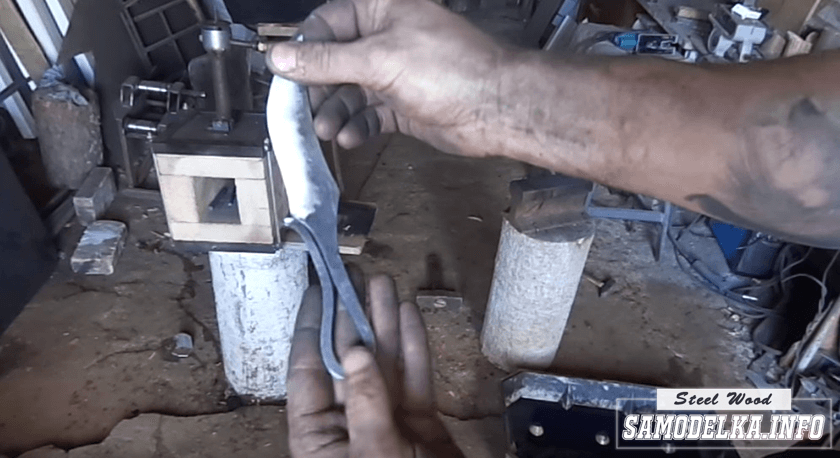

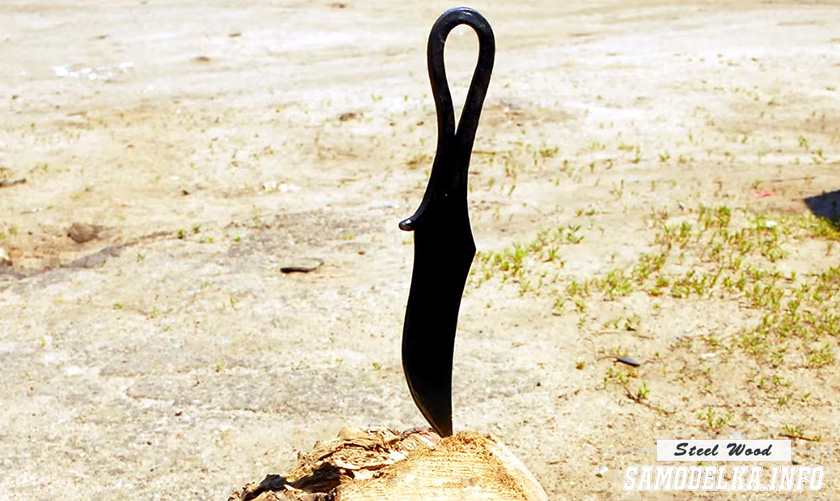
Автор статьи “Нож из обоймы подшипника своими руками” Steel Wood
Смотрите так же:
- самодельный станок для заточки ножей
- самодельное приспособление для заточки сверл малого диаметра
- пила для бетонной тротуарной плитки своими руками
- самодельный токарный станок по дереву
- самодельная наборная ручка ножа из бересты
- Ваша статья будет здесь если Вы ее нам пришлете :) [email protected]
- Об авторе
- Новые самоделки автора

Steel Wood
Друзья, подписывайтесь на мой канал в YouTube
https://www.youtube.com/channel/UCTpxthLF5mGs1FlefDjyBqw
Новые самоделки автора Steel Wood (Смотреть все)
- Сделай сам: светильник Юрского периода - 8 сентября 2018
- Стимпанк люстра своими руками - 26 мая 2018
- Подставка для телефона своими руками - 1 марта 2018
Нож из подшипника своими руками
Вопрос задает Валерий, Московская область:
Недавно услышал от знакомого, что из подшипника можно изготовить отличный нож. Меня очень заинтересовало это, поскольку люблю все мастерить своими руками. Хотелось бы подробнее узнать об этой технологии.
Предоставляем слово нашему эксперту:
Подшипники изготовляют из стали высокого качества, поскольку они работают в трудных условиях и не теряют своих характеристик при значительных нагрузках. Если выковать из него нож, можно получить отличный инструмент. Он не потеряет остроты в самых трудных условиях эксплуатации.
Для ковки ножа из подшипника необходимо следовать представленной инструкции:
- При помощи болгарки необходимо отрезать заготовку нужной длины, используя обойму подшипника. Нужно учитывать запас в 1-2 см.
- Полученную заготовку необходимо приварить к прутку арматуры, исполняющей роль рукоятки.
- Ковка осуществляется при достаточно низких температурах, чтобы материал изменился от светло-красного до более темного оттенка.
- Перед закалкой осуществляется обдирка на точиле или при помощи напильника.
- Для улучшения характеристик ножа рекомендуется произвести нормализацию металла. Для этого его разогревают до 750°С, ждут 5 минут и охлаждают на воздухе. Такие манипуляции повторяют 2-4 раза.
- Производится закалка. Чаще всего это осуществляется при температуре 830°С. Для определения подходящего момента для закалки используют магнит. Когда сталь перестала магнититься, можно приступать к данному процессу. Температура плавления поваренной соли составляет 800°С. Поэтому ею посыпают заготовку, чтобы примерно определить момент достижения оптимальных характеристик для закалки.
- Закалка происходит в масле, температура которого достигает 50-60°С. Заготовку помещают в емкость с подготовленным веществом на 1 час. Все это время ее нельзя шевелить и прислонять к стенкам резервуара.
- После закалки проводят отпуск. Нож помещают в духовку при температуре 160-200°С на 2 часа. Для охлаждения просто гасят огонь.
- Для заточки ножа используется алмазные бруски, для шлифовки – алмазная паста. В процессе данной обработки может утратиться до 2 мм толщины заготовки, что вполне нормально.
Если следовать все правильно и в точности следовать инструкции, полученный нож сможет поцарапать стекло. В процессе эксплуатации он не тупится и не разрушается при нагрузках изгибающего характера. Представленным способом легче всего делать нож с накладными рукоятками.
Видео: Ковка ножа из шарика от подшипника
promzn.ru
Закалка ножа из подшипника, "крестьянский" подход / Гостевая / НеПропаду
Закалка.Проблема.
Поскольку я делаю ножи в основном из подшипников от автомобилей, по размеру обычно это диаметр сантиметров 10-15, и начинал полным дятлом, после чисто интуитивных попыток возникли следующие проблемы:• После закалки в воде сталь хрупкая настолько, что разлетается как стекло при сильном ударе
Собственно, все. Остальное все меня устраивало. Но мне хотелось, чтобы «не ржавело», «хорошо резало», «держало заточку», «не раскалывалось».
Болометра у меня нет, «все на глазок», и когда я читаю рекомендации «выдержать два часа при температуре 453 градуса» — это не для меня. В конце концов, плюс-минус твердости или вязкости мне фиолетово. Меня вполне устроит «более-менее» приличное качество по перечисленным параметрам.
Поэтому.
Решение проблемы:
1. Отковываю, обязательно соблюдая следующие условия:
• При нагреве я лучше недогрею, чем перегрею. Стараюсь не накалять до белого свечения, работаю в диапазоне красного-желтого. Лучше я почаще буду совать-вынимать, чем пережгу. • Внимательно следим за деталью, когда лежит в горне: попытка сэкономить и делать одновременно две детали приводит к тому, что или пережжешь, или что-то испортишь. • Нагрелось до красного яркого с кусками желтого свечения – вынимаем• Периодически пшикаем-брызгаем из бутылочки пластиковой (как на шашлык) – лучше видно температуру, где что нагрето, да и угли экономит• Особенно внимательно, когда есть тонкие детали (лезвие, например) – не пережечь!
2. НИ В КОЕМ СЛУЧАЕ НЕ БИТЬ ПО ХОЛОДНОМУ МЕТАЛЛУ!
• Когда куешь, металл пластичен. И по свечению видно, если он начинает остывать. Конечно, хочется за один раз отковать «побольше». Надо бороться с этим искушением. • Как только при ударе молотом (а я все вручную, нет механики) – чувствуешь, что пластичность уменьшается – останавливаемся, греем дальше.
Пояснение: насколько я понял, объясняется все просто. Как только я треснул молотом по подостывшему металлу, возникают микро-трещины, которые плохо «залечиваются» даже хорошим нагревом, и потом по ним все ломается. Вот и все.
3. Собственно, закалка.
Я пробовал в воду. При любых (почти) вариантах – хрупкая сталь получается. Поэтому взял, слил в канистру отработанного машинного (не проблема достать). Читал картинки и про то, какие температуры для каких марок стали… Разбирался в свечениях и цвете металла. Сухой остаток:
• Когда форма детали скована – я стараюсь максимально близко к финальной форме, чтобы поменьше точить, — приступаю к закалке• Нагреваю до (в среднем) цвета-свечения между красным и желтым (на глазок) – но для этого есть обоснования теоретические, скажу ниже, — и опускаю ВЕРТИКАЛЬНО ЗА ХВОСТИК кончиком лезвия вниз быстро-быстро в масло. Держу несколько минут, чтобы полностью остыло. • Нагреваю до темно-красного цвета и закаляю еще раз• Если «ведет» нож, что бывает, — просто искривляется он – нагреваю до темно-красного цвета (минимальная пластичность) и подправляю, если надо, закаляю еще раз. • Кладу рядом с углями на поддон, вырубаю горн – пусть остывает все вместе.
Результат – шикарно все, и без заморочек. Могу подвести длинную базу, но такой повтор закалок с понижением верхней температуры нагрева на опыте дает отличный результат в среднем, независимо от взятого подшипника (японских экзотик не пробовал, брать не буду – в основном наш Автоваз, Уралаз, Камаз, Газ, и пр. Совецкие заводы.)
Теперь теория.
Если мы возьмем картинку переходов разных аустентитов в мартенситы и прочие цементиты,
… то обратим внимание, что В СРЕДНЕМ диапазон правильного нагрева выше 850, но ниже 900 градусов. Поэтому нагревать надо примерно до диапазона цветов как на картинке ниже. Повтор ХУЖЕ не делает, а ЛУЧШЕ делает. Вот и все.
Поскольку подход этот «крестьянский» я его излагаю просто и все.
nepropadu.ru
Клинок ножа из подшипника - Изготовление ножа - Как сделать нож - Каталог статей
Клинок ножа из подшипника. Клинок из подшипника. Клинок из подшипника в домашних условиях. Мы заимели все необходимое, чтобы начать ковать. Но подшипник закален, и начать сразу ковать то в дальнейшем это вылезет очень неприятными косяками. А может и не вылезет. Но лучше перестраховаться. Чтобы не полезли косячки - производим отжиг. Берем полешко (не смолистое) и при помощи топора превращаем в небольшие лучины. Складываем их в горне и засовываем вниз бересту или газету. Поджигаем. Ждем пока разгоритсяДля отжига очень важен равномерный прогрев и медленное охлаждение. ОЧЕНЬ МЕДЛЕННОЕ. Горн у меня кирпичный и сперва большая часть теплоты поглощается кирпичами, и нагреть заготовку проблематично. Поэтому минут 10-15 просто сжигаем уголь, прогреваем горн.
Горн прогрелся, время пришло. закладываем под завязку углей а сверху кучи - наш подшипник. Не суйте его сразу в самое пекло, неравномерно нагреется. Не столь важна равномерность по поверхности сколько внутри. Итак заготовка лежит в горне на куче угля. Она сама опустится в пекло, по мере сгорания топлива. Нужно только иногда ее поправлять да изредка уголь добавлять.
На следующий день, после того как заложили в горн заготовку раскапываем все это дело и внимательно осматриваем на наличие всяческих видимых дефектов (вдруг чё). Проверяем напильником, если берется легко - то отлично, если скользит и не цепляет - заново отжигаем.
Как видим - окалины почти нет, в моем случае. Зола справилась и с функцией теплоизолятора и не пустила лишний кислород к подшипнику.
Мы имеем отожженный подшипник, его надо разделать. Можно разрезать болгаркой, но у меня под рукой нет ничего такого. Поэтому греем одну сторону заготовки, неважно какую, он же круглый.
Обращу Ваше внимание на то, что при рубке коротким зубилом горячих заготовок руку обжигает ИК излучением и конвекцией. Поэтому зубило я немного оттюнинговал. А точнее присобачил на него экран из 4мм резины. Очень эффективен однако.
Итак заготовка нагрелась, вынимаем и кладем на наковальню, рубим там где горячее. После первого, несильного нагрева имеем это:
Снова греем, снова рубим. За 4 нагрева разрубаем большое кольцо.
Греем, несем в тиски, зажимаем, разгибаем плоскогубцами
Начинаем расковывать.
Ширину заготовки хочу увеличить следующим способом: красный цвет-кованые спуски, синий-слесареные.
Процесс ковки греем заготовку с одной и с другой стороны. Начинаем оттягивать хвостовик.
и вытянули репку готовый хвост
Так как ширина заготовки 25мм а у клинка по плану 20, то клинок тянем так же как и хвостовик.
Монотонность вытяжки пропускаем, и так все уже ясно. Обрубаем лишнее из расчета на правку острия, мех. обработку и передвижение плечиков при слесарке.
Правим острие, и выравниваем плоскость. Проверяем прямоту клина
Ну и собственно готовый на данной стадии клин и эскиз. Клин изготовлен с запасом 1-2мм на слесарку.
Приступаем к самой нудной (ИМХО) части проекта. Слесарная обработка. Сначала выравниваем обух, он будет БАЗОВОЙ гранью. Для этого зажимаем клинок в тиски так, чтобы губки не дали проскочить и снять лишнего. Одновременно они служат направляющими для выведения прямого обуха.
Когда обух готов приступаем к будущей режущей кромке. Постоянно сверяемся с наброском проекта а так же контролируем при помощи штангенциркуля (далее ШЦ) ширину клинка. Делаем с запасом примерно 0,2 на чистовцю обработку.
Когда очертания клинка стали совпадать с шаблоном начинаем оформлять плечики. Опять используем тиски как ограничитель. В результате должно получиться что-то вроде этого
Используем ШЦ как угольник и от обуха как от базы отчерчиваем линию
Формируем второе плечо
Далее надо выровнять плоскости боковых сторон, но надежно закрепить заготовку в тисках неудастся, потому прибегаем к хитрости. Берем ровный кусок деревяшки и 3 кровельных самореза (у кровельных есть шайбочки с резиновыми подкладками) и прикручиваем клинок к деревяшке
Начинаем сводить плоскость напильником. Одна сторона готова
Вторую сторону ровняем точно так же. Проверяем ШЦ толщину в разных местах и если надо корректируем.
Клинок стал тоньше хвостовика. Это нехорошо Ровняем хвостовик. К тому же он должен к своему кончику сходить клином, причем в обоих плоскостях. Для того, чтобы случайно не заехать на клинок я вбил гвоздики
После серфинга по тематическим сайтам и прочтения нескольких статей пришёл к выводу что на туристическом ноже (как мне и говорили неоднократно) наиболее уместны прямые спуски. Ну я и начал их делать.
Собственно процесс: Начинаем с того, что сводим риски от грубого напильника, я использовал крупнозернистую шкурку (сколько грит не знаю). Оторвал кусок шириной 5см и проткнул хвостом напильника.
Ну и так же как и при выравнивании плоскостей начал сводить риски. Сводим ВСЕ риски от напильника. Даже одна единственная может существенно испортить внешний вид. Небольшие каверны я оставил, они снимутся при сведении спусков.
Далее разметка. Берем маркер, но лучше раствор медного купороса (более стойкий). Заштриховываем будущую РК
Для того чтобы металл непогорел при закалке нужно оставить на РК порядка 1мм толщины (при толщине клинка около 3мм) У меня клин 2,8мм следовательно надо убрать по 0,9 мм с каждой стороны. Выставляем на ШЦ 0,9 и отчерчиваем линии. проводить можно только ОДИН РАЗ, иначе линия получится нечеткой а то и вовсе двойной. Поэтому хорошенько прижимаем и ведем
Теперь определяем высоту спусков. Я выставил на ШЩ 12 мм. Заштриховываем примерную область линии и отчерчиваем
Круглым надфилем формируем примерную границу спусков
И начинаем мудохатся с напильником
С другой стороны все точно так же. Ну и результат
После предыдущих фотографий над клином еще поработал, спуски стали ровнее. А сегодня - закалил. Вечером приступил к работе. Прогреваем горн дровами
Греем клин. Далее у меня кончились руки, фотографировать было некому, и самое интересное осталось за кадром.
Суть такова. Греем примерно до 850 градусов, для ориентира взял вот такую табличку судя по ней нам нужен алый цвет свечения. Для контроля можно применить еще 1 способ. Проверка нагрева магнитом. Когда сталь проходит критическую точку и перестает магнитится - она готова.
В общем, применяя эти 2 способа и контролировал нужную температуру. Столкнулся с проблемой, горн греет сильнее у первых отверстий, чем у дальних, но решил проблему возвратно-поступательными движениями клина вдоль фурм, нагрев получился как никогда равномерный.
Далее начал потихоньку слесарить дальше, использую обычную "лодочку" .
Результат меня поразил. Получается ровная плоскость, но занятие - та еще медитация. Но мне понравилось, даже сам не знаю почему 2,5 часа работы. Главное - фон настроить, радио там или телевизор. В общем, "лодочка" как инструмент мне нравится. Не ожидал, чесно
Я использую такой горн.
Допустим горн у Вас уже есть, но на чем ковать? Какое топливо использовать? Опытные мастера рекомендуют использовать древесный уголь. Я с ними солидарен, так как в силу своей будущей профессии знаю, что каменный уголь и кокс содержат серу и фосфор, которые охрупчивают сталь, не добавляя ей никаких полезных свойств. Древесный же уголь этих элементов если и содержит - то ооооооооочень мало. Кроме того у древесного угля есть еще один жирный плюс - доступность. Простому обывателю трудно раздобыть кокс или каменный уголь в малых количествах (менее 100кг не видел объявлений). А древесный можно купить в любом супермаркете. В нашем городе 2,5кг пачка стоит ~50р. Мне ее хватает на 1 клинок без термообработки (далее ТО). Для меня это приемлемо. Для тех же кто не может купить уголь по каким либо причинам. Уголь можно довольно легко сделать:
Копаем яму примерно метр глубиной (можно и глубже) и примерно метр диаметром. Разводим на дне костер и закладываем дрова. Полешки должны быть одинаковой толщины и длины. Подкладываем дрова пока яма не заполнится углем наполовину. Обильно поливаем водой, если не хотим получить золу. ОБИЛЬНО. Вынимаем топливо из ямы и опять водные процедуры. Нужно отделить ресурс от золы и грязи. Далее выкладываем уголь небольшим слоем на открытое, проветриваемое и солнечное место и сушим.
Способ второй (для тех, кто имеет 200 литровую стальную бочку). Бочка должна быть открыта с одной стороны (не пробка, а вся плоскость). Закладываем дрова в бочку, пересыпая слои песком и утрамбовывая (кислород не должен добраться до дров). Снаружи обкладываем сие сооружение большим количеством топлива. Нужно прокалить дрова в бочке , довольно долго. Костер должен пылать около 4-х часов. После остывания вынимаем получившийся уголь вместе с песком и опять-же промываем и сушим.
Итак у нас есть горн, есть топливо. Нужно чем-то и на чем-то ковать. Идеально конечно иметь наковальню, но это ,увы, редкость. Можно использовать отшлифованный обрезок рельса. Я использую кувалду, закрепленную на чурбачке. Вот она:
Это крайний вариант.
Для ковки так же необходим и молот. Я использую старый, советский, еще от деда остался. По словам отца боек был сантиметра на 2 длиннее. Для более точной ковки я использую слесарный молоток (у слесарного, в отличие от плотницкого боек круглый, и за счет этого на металле остаются не такие заметные вмятины) Вот собственно и молотки:
Но заготовку, разогретую да +1200 градусов руками не удержать. Я использую плоскогубцы, наращенные трубками, но можно сотворить клещи.
paromon.ucoz.ru
Как сделать нож из подшипника - Изготовление ножа - Как сделать нож - Каталог статей
Как сделать нож из подшипника. Нож из подшипника. Вот посмотрите нож с нуля откованный и собранный мною, в прошлом году из стали ШХ-15 Подшипник.Шх стали, обычно калится на 50-60 градусов выше других сталей. Так как у меня, не с чем определить соответствующую температуру, я делал закалку на цвет. Заготовку клал в горн, острием вниз. Когда цвет на острие достигал яркомалинового, с легкой желтизной цвета, а на обухе малинового, я опускал его в подогретое трансмиссионное масло, до 70 градусов. А потом снимал напряжение , доводя клинок, до состояния легкой побежалости и остужал его на кирпичике, рядом с горном.
Закалка и доводка. Вроде закалил, стекло слегка царапает….. Появился интересный, какой-то рисунок.
Сборка ножа. Значит так ! Я перепробовал всевозможные сборки рукояти и остановился, на вышеизложенном. Да он трудоемкий и требует определенного мастерства и наличие соответствующих инструментов…. Метчики, плашки длинные сверла, а самое главное горелки для сварки газом «МАФ» …. Я всегда, к хвостовику клинка довариваю, допаиваю толстостенную медную, латунную или нерж. трубу …. До 6 мм. Сначала на конце нарезаю резьбу, под гайку и стягиваю рукрять. Что и Вы увидели, на фото выше….. После обработки рукояти, я срезаю, стянутый тыльник в ноль и в трубе нарезаю резьбу, под болт темляка и стягиваю им рукоять.
А дерево вырезал в лесу.... Наверно Баярешник.
Ножны для ножа своими руками.
paromon.ucoz.ru
Нож из подшипника | Справочник конструктора-машиностроителя
Обойму разрезаю болгаркой, гррею до ковочной температуры, хорошо 900 - 1000 гр, пневмомолота нет, кую вручную, по сравнению с другими металлами, например, с напильником ШХ кажется тверже при ковке.Довожу в орму пластины до определенной толщины или сообщаю форму клинка, окончательно нагреваю до 800 - 1000 гр и оставляю остывать вместе с горном.
8658303.jpg"http://www.youtube.com/embed/eMoOesO8lAA" frameborder="0"/>
при отпуске 300С углеродистые и малолегированые стали хрупкими становятся .... насчёт синеломкости - хрупкости первого рода, здесь рассказывать по разному можно, всё-таки на 200 бывает хрупковато, и у любой стали есть близкая ямка падения ударной вязкости, в справочниках попадаеться зависимость от порядков, часто на узком участке, градусов 40, зависит ещё от времени выдержки - правда здесь не уверен, давно, подзабыл.В общем из практики, делал ножи на труборез, из всего, 65Г, ШХи, так делаешь отпуск около 200, крошаться, 300 - делают, ну здесь конечно набор изменений, но всё - же.Maksimak, после ковки либо отожгите а проще нормализуйте несколько ( 4 - 7 ) раз ориентируясь на магнитик, без выдержки, обдерите начерно нож и лишь затем калите.Если заготовка мелкая нужны ступеньки или промежуточные короткие отжиги на 620.
Вот и все.Теперь подшипник нужно достать из колес и заняться промыванием и смазкой.Не надо стопроц. верить тем, кто недвусмысленно советует "просто купить новейшие да и все тут" - персонально у меня целый процесс снятие колес - промывка - смазка - сборка занимает немного более часа.В главный раз, конечно, у Вас вйдет подольше.
spravconstr.ru