Углеродное волокно – характеристики и особенности хранения. Углеволокно что такое
Углеволокно Википедия
Углеродное волокно — материал, состоящий из тонких нитей диаметром от 5 до 15 мкм, образованных преимущественно атомами углерода. Атомы углерода объединены в микроскопические кристаллы, выровненные параллельно друг другу. Выравнивание кристаллов придает волокну большую прочность на растяжение. Углеродные волокна характеризуются высокой силой натяжения, низким удельным весом, низким коэффициентом температурного расширения и химической инертностью.
Углеродное волокно Углеродная лентаИстория
Впервые получение и применение углеродных волокон было предложено и запатентовано в 1880 г. американским изобретателем Эдисоном для нитей накаливания в электрических лампах. Эти волокна получались в результате пиролиза хлопкового или вискозного волокна и отличались высокой пористостью и хрупкостью.
Вторично интерес к углеродным волокнам появился, когда велись поиски материалов, пригодных для использования в качестве компонентов для изготовления ракетных двигателей. Углеродные волокна по своим качествам оказались одними из наиболее подходящих для такой роли армирующими материалами, поскольку они обладают высокой термостойкостью, хорошими теплоизоляционными свойствами, коррозионной стойкостью к воздействию газовых и жидких сред, высокими удельными прочностью и жёсткостью.
В 1958 г. в США были получены УВ на основе вискозных волокон. При изготовлении углеродных волокон нового поколения применялась ступенчатая высокотемпературная обработка гидратцеллюлозных (ГТЦ) волокон (900 °C, 2500 °C), что позволило достичь значений предела прочности при растяжении 330—1030 МПа и модуля упругости 40 ГПа. Несколько позднее (в 1960 г.) была предложена технология производства коротких монокристаллических волокон («усов») графита с прочностью 20 ГПа и модулем упругости 690 ГПа. «Усы» выращивались в электрической дуге при температуре 3600 °C и давлении 0,27 МПа (2,7 атм). Совершенствованию этой технологии уделялось много времени и внимания на протяжении ряда лет, однако в настоящее время она применяется редко ввиду своей высокой стоимости по сравнению с другими методами получения углеродных волокон.
Почти в то же время в СССР и несколько позже, в 1961 г., в Японии были получены УВ на основе полиакрилонитрильных (ПАН) волокон. Характеристики первых углеродных волокон на основе ПАН были невысоки, но постепенно технология совершенствовалась и уже через 10 лет (к 1970 г.) были получены углеродные волокна на основе ПАН-волокон с пределом прочности 2070 МПа и модулем упругости 480 ГПа. Тогда же была показана возможность получения углеродных волокон по этой технологии с ещё более высокими механическими характеристиками: модулем упругости до 800 ГПа и пределом прочности более 3 ГПа. УВ на основе нефтяных пеков были получены в 1970 г. также в Японии.
Углеродная ткань плотностью 200 гр/м2Чэнь и Чун исследовали эффект углеродного волокна с добавкой кремнезема на усадку при высыхании бетона и пришли к выводу, что объемное соотношение углеродного волокна в количестве 0,19% (при средней длине волокна 5мм и диаметре 10 мкм) с отношением микрокремнезема, равным 15% от массы цемента, вызывало снижение усадки при высыхании до 84%. Исследователи обнаружили, что использование углеродного волокна с микрокремнеземом позволяет улучшить такие свойства, как прочность при сжатии и химическая стойкость[1].
Алхадиси Абдул Кадир и др. исследовали влияние добавки углеродного волокна на механические свойства легкого бетона. Волокно было добавлено в соотношении 0,5% 0,1%, 1,5% по объему. Все составы характеризовалось повышенной прочностью на сжатие и прочностью на разрыв, а также сопротивлению изгибу около 30% , 58% и 35%, соответственно, по сравнению с эталонной смеси[2].
Получение
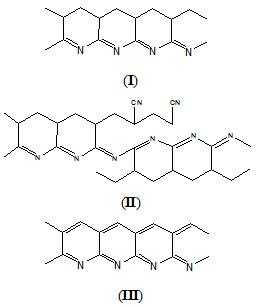
Рис. 1. Структуры, образующиеся при окислении ПАН-волокна
УВ обычно получают термической обработкой химических или природных органических волокон, при которой в материале волокна остаются главным образом атомы углерода. Температурная обработка состоит из нескольких этапов. Первый из них представляет собой окисление исходного (полиакрилонитрильного, вискозного) волокна на воздухе при температуре 250 °C в течение 24 часов. В результате окисления образуются лестничные структуры, представленные на рис. 1. После окисления следует стадия карбонизации — нагрева волокна в среде азота или аргона при температурах от 800 до 1500 °C. В результате карбонизации происходит образование графитоподобных структур. Процесс термической обработки заканчивается графитизацией при температуре 1600-3000 °C, которая также проходит в инертной среде. В результате графитизации количество углерода в волокне доводится до 99 %. Помимо обычных органических волокон (чаще всего вискозных и полиакрилонитрильных), для получения УВ могут быть использованы специальные волокна из фенольных смол, лигнина, каменноугольных и нефтяных пеков.
Дополнительная переработка УВ
Углеродные волокна могут выпускаться в разнообразном виде: штапелированные (резаные, короткие) нити, непрерывные нити, тканые и нетканые материалы. Наиболее распространенный вид продукции — жгуты, пряжа, ровинг, нетканые холсты. Изготовление всех видов текстильной продукции производится по обычным технологиям, так же как для других видов волокон. Вид текстильной продукции определяется предполагаемым способом использования УВ в композиционном материале, точно так же, как и сам метод получения композита. Основные методы получения композитов, армированных углеродными волокнами, являются обычными для волокнистых материалов: выкладка, литье под давлением, пултрузия и другие. В настоящее время выпускается ряд видов УВ и УВМ, основные из которых перечислены ниже.
- На основе вискозных нитей и волокон:
- нити, ленты, ткани;
- нетканый материал; Файл:Углеродный войлок
- активированные сорбирующие ткани;
- активированные сорбирующие нетканые материалы.
- На основе вискозных штапельных волокон:
- волокна и нетканые материалы: карбонизованые и графитированые;
- На основе ПАН-нитей и жгутов:
- ленты и ткани ;
- активированные сорбирующие волокна и нетканые материалы;
- дисперсный порошок из размолотых волокон.
- На основе ПАН-волокон:
- Волокна и нетканые материалы: карбонизованные и графитированные.
Свойства
УВ имеют исключительно высокую теплостойкость: при тепловом воздействии вплоть до 1600—2000 °С в отсутствие кислорода механические показатели волокна не изменяются. Это предопределяет возможность применения УВ в качестве тепловых экранов и теплоизоляционного материала в высокотемпературной технике. На основе УВ изготавливают углерод-углеродные композиты, которые отличаются высокой абляционной стойкостью. УВ устойчивы к агрессивным химическим средам, однако окисляются при нагревании в присутствии кислорода. Их предельная температура эксплуатации в воздушной среде составляет 300—370 °С. Нанесение на УВ тонкого слоя карбидов, в частности SiC, или нитрида бора позволяет в значительной мере устранить этот недостаток. Благодаря высокой химической стойкости УВ применяют для фильтрации агрессивных сред, очистки газов, изготовления защитных костюмов и др. Изменяя условия термообработки, можно получить УВ с различными электрофизическими свойствами (удельное объёмное электрическое сопротивление от 2·10−3 до 106 Ом/см) и использовать их в качестве разнообразных по назначению электронагревательных элементов, для изготовления термопар и др.
Активацией УВ получают материалы с большой активной поверхностью (300—1500 м²/г), являющиеся прекрасными сорбентами. Нанесение на волокно катализаторов позволяет создавать каталитические системы с развитой поверхностью.
Обычно УВ имеют прочность порядка 0,5—1 ГПа и модуль 20—70 ГПа, а подвергнутые ориентационной вытяжке — прочность 2,5—3,5 ГПа и модуль 200—450 ГПа. Благодаря низкой плотности (1,7—1,9 г/см³) по удельному значению (отношение прочности и модуля к плотности) механических свойств лучшие УВ превосходят все известные жаростойкие волокнистые материалы. Удельная прочность УВ уступает удельной прочности стекловолокна и арамидных волокон. На основе высокопрочных и высокомодульных УВ с использованием полимерных связующих получают конструкционные углеродопласты. Разработаны композиционные материалы на основе УВ и керамических связующих, УВ и углеродной матрицы, а также УВ и металлов, способные выдерживать более жёсткие температурные воздействия, чем обычные пластики.
Применение
УВ применяют для армирования композиционных, теплозащитных, химостойких и других материалов в качестве наполнителей в различных видах углепластиков. Наиболее ёмкий рынок для УВ в настоящее время — производство первичных и вторичных структур в самолетах различных производителей, в том числе таких компаний как «Boeing» и «Airbus» (до 30 тонн на одно изделие). По причине резко возросшего спроса в 2004—2006 гг. на рынке наблюдался большой дефицит волокна, что привело к его резкому подорожанию.
Из УВ изготавливают электроды, термопары, экраны, поглощающие электромагнитное излучение, изделия для электро- и радиотехники. На основе УВ получают жёсткие и гибкие электронагреватели, в том числе ставшие популярными т. н. «карбоновые нагреватели», обогревающие одежду и обувь. Углеродный войлок — единственно возможная термоизоляция в вакуумных печах, работающих при температуре 1100 °C и выше. Благодаря химической инертности углеволокнистые материалы используют в качестве фильтрующих слоёв для очистки агрессивных жидкостей и газов от дисперсных примесей, а также в качестве уплотнителей и сальниковых набивок. УВА и углеволокнистые ионообменники служат для очистки воздуха, а также технологических газов и жидкостей, выделения из последних ценных компонентов, изготовления средств индивидуальной защиты органов дыхания. Широкое применение находят УВА (в частности, актилен) в медицине для очистки крови и других биологических жидкостей. В специальных салфетках для лечения гнойных ран, ожогов и диабетических язв — незаменима ткань АУТ-М, разработанная в начале 80-х годов и опробованная при боевых действиях в Афганистане[3]. Как лекарственное средство применяют при отравлениях (благодаря высокой способности сорбировать яды. Например препарат «Белосорб», или АУТ-МИ на основе светлогорского сорбента), как носители лекарственных и биологически активных веществ. УВ катализаторы используют в высокотемпературных процессах неорганического и органического синтеза, а также для окисления содержащихся в газах примесей (СО до CO2, SO2 до SO3 и др.). Широко применяется при изготовлении деталей кузова в автоспорте, а также в производстве спортивного инвентаря (клюшки, вёсла, лыжи, велосипедные рамы и компоненты, обувь) и т. д.
Углеволокно применяется в строительстве в различных системах внешнего армирования (СВА) — при его помощи усиливают железобетонные, металлические, каменные и деревянные конструктивные элементы зданий и сооружений с целью устранения последствий разрушения материала и коррозии арматуры в результате длительного воздействия природных факторов и агрессивных сред в процессе эксплуатации, а также для сейсмоусиления. Суть данного метода заключается в повышении прочности элементов, воспринимающих нагрузки в процессе эксплуатации зданий и сооружений, с помощью углеродных тканей, ламелей и сеток. Усиление строительных конструкций углеволокном повышает несущую способность без изменения структурной схемы объекта.
См. также
Примечания
Ссылки
- С. Симамура. Углеродные волокна. М.: «Мир», 1987.
- Конкин А. А., Углеродные и другие жаростойкие волокнистые материалы, М., 1974.
- Время углеродного волокна
wikiredia.ru
Углеродное волокно – характеристики и особенности хранения.
В наиболее ответственных изделиях применяют углекомпозиты (углепластики). Согласно расчетам, среди всех возможных соединений, на основе периодической системы элементов, графит имеет самые высокие прочностные и термические характеристики. Углеродное волокно имеет один из наиболее высоких показателей по удельной прочности среди других волокон. Имеет высокую стойкость к кручению и усталости. Уступая лишь в ударной прочности арамиду и стеклу.
Углеродное волокно-производство
Столь высокую стоимость углеродного волокна обуславливает сложность и энергоемкость процесса его получения. Смысл процесса состоит в поэтапной чистке углеродосодержащих нитей от ненужных атомов, оставляя в конце процесса до 99% углерода в объеме нити.
УВ получают путем термического разложения (пиролизом) исходных нитей: гидратоцеллюлозных, полиакрилонитрильных (ПАН). Так же нефтяных или каменноугольных пеков. В настоящее время, промышленное значение имеет производство УВ на базе вискозы или ПАН.
Процесс получения УВ на основе ПАН
Следует заметить, что химический состав и структура УВ зависит от состава исходного сырья.
В первую очередь, полиакриловые жгуты подвергают окислению, проводя термическую обработку на воздухе при температуре 250-350 °С.
Окисленный ПАН так же представляет интерес в некоторых сферах производства как термостойкий и трудно горючий материал.
После окисления, полотно проходит через печи карбонизации (700-1500 °С) и графитизации (1500—3000 °С). На этой стадии удаляются остатки водорода и гетероатомов, происходит образование двойных связей между атомами углерода. Процессы карбонизации и графитизации проводятся в инертной среде (чаще всего в среде азота).
В завершении процесса карбонизации (в некоторых случаях стадия графитизации может исключаться) жгут имеет готовый химический состав и структуру, но проходит еще ряд этапов для повешения адгезии с матрицей:
— обработка поверхности: для повышения внутренней поверхности наиболее часто используется метод жидкофазного электрохимического окисления (ЭХО). Суть метода в прохождении жгутов через ванну с электролитом и одновременным прохождением тока через сами жгуты, точнее жгут является анодом, а вал, по которому он проходит, катодом. Протекающий ток выделяет из электролита атомы кислорода. Атомы кислорода вступают в реакцию с углеродом, происходит химическая обработка материала. Поверхность карбонового полотна вследствие данной реакции становится «шероховатой». Обнажая атомы углерода и создавая свободные функциональные группы способные к ионному обмену.
— нанесение ПАВ (поверхностно активное вещество). Оно же, так называемое аппретирование. В качестве аппрета чаще наносятся эпоксидные смолы без отвердителя. Аппрет защищает от истирания в процессе хранения, транспортировки и текстильной переработки. Вытесняет из пор влагу и воздух.
Этап сушки после нанесения аппрета является завершающим этапом, после которого жгуты наматываются на бобины (обычно массой до 8 кг).
Характеристики углеродного волокна
Модуль упругости. УВ обычно группируются в соответствии со своим модулем:
- Низкомодульное (HS): 160-270 ГПа;
- Средний модуль (IM): 270-325ГПа;
- Высокомодульное (НМ): 325-440 ГПа;
- Сверхвысокий модуль (UHM): 440+ ГПа;
Диаметр и количество элементарных нитей. Каждый жгут состоит из тысяч элементарных нитей (филаментов). Диаметр такой углеродной нити: 5-7 мкм, что в 2-3 раза тоньше человеческого волоса. В маркировке у любого типа волокна есть обозначения: 3К, 6К, 12К, 24К- это и есть количество филаментов в жгуте (в тысячах).
Линейная плотность. Кроме обычной плотности, у волокон принято выделять так же линейную. Измеряется она в тексах (tex). Если линейная плотность указана 800 tex, значит, километр этого жгута имеет массу 800гр.
Прочностные характеристики
Итоговое значение прочности, указываемое в сертификатах качества и т.д. снимается уже с пропитанного и отвержденного жгутика (микропластика). Микропластик- жгут пропитанный полимерным связующим и отвержденный при воздействии растягивающего напряжения.
УВ достаточно хрупкое поэтому не имеет большого смысла снимать с него прочностные характеристики в непропитанном виде. Так же, для конечного потребителя важнее знать свойства углеродного волокна в отвержденной полимерной матрице, то есть в композите. Поэтому в чаще всего указывают:
- Прочность при растяжении комплексной нити в микропластике. ГПа
- Модуль упругости при растяжении комплексной нити в микропластике. ГПа
Условия транспортировки и хранения углеродного волокна
- Бобины должны храниться в крытых складских помещениях в упакованном виде, коробки должны находиться в горизонтальном положении.
- Рекомендуемые условия хранения.
- Температура: 0-40 °С. Хранение при минусовой температуре не рекомендуется.
- Влажность: 40-80%.
- Допускается перевозка в неотапливаемом транспорте при температуре до -30 °С.
- Во избежание конденсации влаги на поверхности. Перед использованием, нераспакованные бобины должны быть выдержаны не менее 48 часов при температуре от 20 до 30 °С и влажности от 40 до 80%.
- При правильных условиях хранения, производитель гарантирует сохранность свойств в течение 2 лет с даты производства.
Заключение
Надо понимать, УВ не является гарантией качества и гарантией сверх прочностных свойств изделия. Сами по себе углеродные нити довольно хрупкие и ломкие. Без правильных условий полимеризации или при не правильном подборе матрицы или ее не совместимости с нитью можно и не достигнуть заявленных производителем свойств. К тому же УВ уступает базальту и стеклу в некоторых видах мех. испытаний. При том, что даже самое дорогое стекло и базальт в 10ки раз дешевле, чем самое дешевое углеродное волокно. В дополнение ко всему, по причине широкого применения углеродных волокон в оборонной промышленности, для того чтобы купить его за рубежом напрямую у производителя необходимо получение лицензии.
composite-materials.ru
Применение углеволокна в строительстве | ИнноваСтрой
Немного истории: как появился карбон
На сегодняшний день углерод в том или ином виде востребован практически во всех промышленных отраслях. Особенностью и главным его преимуществом является то, что он способен гармонично дополнять традиционные строительные материалы, будь то стекло, метал, дерево или бетон или же и вовсе заменить их, что весьма выгодно и для человека, и для природы.
Открыт углерод еще в 1880 году Т. Эдисоном в процессе исследования нити лампы накаливания. Благодаря зарубежным производителям и промышленникам углеволокно стало активно применяться в различных отраслях, в том числе и в строительстве. На территории нашей страны последние проекты с использованием углеволокна разрабатывались еще в советские времена, потому сейчас они активно реанимируются инженерами.
Углеволокно: характеристика материала и особенности его использования
Углеродное волокно является продуктом искусственного происхождения и относится к полимерам с композитной структурой. Формируется из тонких нитей (диаметр от 3 до 15 микрон), а нити, в свою очередь, из атомов углерода, которые объединяются в кристаллическую сетку. За счёт физических особенностей атома углерода, кристаллы в сетке располагаются параллельно относительно друг друга. Такое выравнивание является ключевым фактором, который способствует повышенной прочности волокна на растяжение.
Широкое использование углеволокна в аэрокосмической сфере и оборонной промышленности, а также для сооружения зданий обосновано тем, что по твердости материал значительно превосходит металл. Углеволокно в строительстве начали использовать в 1980 году в Калифорнии для укрепления построек, находящихся в сейсмически активной зоне. В отечественном строительстве материал применяется, как правило, в процессе ремонтных работ, но его популярность и сфера использования постепенно растет.
Технические характеристики и плюсы применения в строительстве
Столь продолжительный эксплуатационный срок углеволокна обусловлен такими характеристиками:
- Отличная адгезия к поверхностям с различной структурой.
- Высокая устойчивость к коррозийным процессам.
- Лёгкость и прочность. Благодаря тому, что углеволокно обладает поразительной лёгкостью, его используют в системах армирования, что позволяет снизить нагрузку на фундамент здания.
- Изоляция от влаги. Поверхность углепластикового волокна является глянцевой, что исключает возможность его реакции с водой.
- Высокая огнеупорность и ударопрочность.
- При использовании для армирования, можно наносить материал в несколько слоёв.
- Проведение ремонтных работ любого типа, где возможно применение углеволокна, может осуществляться без прекращения эксплуатации самого здания.
- Является полностью токсически безопасным и экологически чистым.
- Высокая степень универсальности. Может использоваться при армировании конструкций практически любых конфигураций: на ребристых поверхностях, закругленных и угловых элементах, балочных сегментах рамных конструкций и пр.
Составляющей углеродного волокна является полиакрилнитрит, который предварительно обрабатывается высокой температурой (в пределах 3000° - 5000°С). Учитывая вышеописанные технические характеристики, наиболее частой сферой применения углеволокна в строительстве является внешнее армирование.
При этом волокно пропитывается двухкомпонентной эпоксидной смолой, которая выступает связующим веществом. Монтаж производится аналогично обоям – материал просто наклеивается на поверхность конструкции, которая укрепляется.
Использование именно эпоксидной смолы в качестве связующего вещества обусловлено следующими особенностями материала:
- Такая смола имеет высокие адгезивные свойства по отношению к бетонным поверхностям.
- Компоненты углеволокна и смолы вступают между собой в химическую реакцию, в результате которой углеводород приобретает жёсткость пластика и становится прочнее стали в 7 раз.
Благодаря таким характеристикам углеволокно занимает лидирующие позиции среди композитных материалов. Прочность материала на разрыв в 4 раза превосходит сталь лучших марок, несмотря на то, что он на 75% легче железа и на 30% алюминия. Удельный вес углеродного волокна относительно низкий, а при нагревании материал расширяется незначительно, что обеспечивает возможность применение углеволокна в различных климатических зонах.
Недостатки углеволокна
Список недостатков карбона короткий, но обязательно должны быть учтены при планировании строительства. Выделяют три основных недостатка:
- Углеволокно является хорошим отражателем электрических волн.
- Материал отличается высокой стоимостью в сравнении с аналогами.
- Изготовление композита более трудоёмкое, чем производство металла.
Применение углеродного волокна в строительстве: основные варианты
Эффективность карбона позволяет успешно применять его для армирования конструкций из дерева, кирпича или железобетона. Согласно СНиП и ГОСТ, сооружение, усиленное таким материалом, становится прочнее на сжатие до 120%, а на изгиб получает еще плюс 65% прочности.
Помимо такого варианта использования, углеродное волокно также успешно используется для реставрации каменных конструкций, к примеру, балок и опор бетонных мостов. В частном строительстве усиление фундамента или стен посредством карбона придаст сооружению большой запас прочности.
Усиление построек с помощью армирования карбоном необходимо в таких случаях:
- Конструкция была повреждена, в результате чего её несущая способность снизилась, стали появляться трещины.
- Изменились условия эксплуатации помещения, возросли нагрузки на него.
- Планируется постройка здания в сейсмически активной зоне.
- Для устранения разрушений бетона и коррозийных процессов в арматуре, если постройка долгое время подвергалась агрессивному воздействию внешней среды.
Если углеродное волокно было выбрано на этапе проектирования постройки, как один из компонентов системы внешнего армирования, то в работе следует руководствоваться Сводом правил 164.1325800.2014.
Производя армирование самостоятельно, нужно учитывать, что наклеивание карбона осуществляется в зонах наибольшей нагрузки: как правило, это центральная часть пролета, которая соприкасается с нижней гранью. Для работы с изгибами можно выбрать любой тип материала – ленты, сетки или ламели.
В процессе армирования балок может возникнуть необходимость дополнительного укрепления приопорных зон, что повысит несущую способность всей конструкции при поперечной нагрузке. Для этого используют U-образные хомуты из лент или сеток.
Где следует осуществлять внешнее армирование карбоном
Углеволокно в строительстве может быть использовано для усиления зданий и сооружений из таких материалов:
- Камень. Сюда относят столбы, пилоны, кирпичные дома. Углеволокно применимо здесь как в процессе постройки, так и для проведения рементных работ.
- Железобетон. Здесь углеродное волокно может быть использовано для гидротехнических построек, мостов, паток архитектуры.
- Металл. Такие сооружения имеют близкий к углеволокну модуль прочности и упругости, но их усиление все равно необходимо, особенно в зонах с неустойчивыми грунтами.
Условия успешного процесса армирования внешних конструкций
Чтобы процесс усиления постройки прошёл максимально эффективно, следует обеспечить ряд таких условий:
- Надежное сцепление с поверхностью здания. Чем лучше армирующая сетка из углеволокна будет приклеена к конструкции, тем более эффективной будет передача усилий на неё.
- Отсутствие естественной влаги. Важно обеспечить сухость поверхности, армирование которой будет проводиться.
- Материалы, используемые в работе (особенно клеевые составы) должны отличаться высоким качеством и отличными характеристиками для обеспечения максимальной эффективности.
Профессиональное внешнее армирование углеволокном
Несмотря на возрастающую популярность использования углеродного волокна, технология его применения остаётся достаточно сложной для домашнего мастера. Потому если вы хотите осуществить строительные или ремонтные работы с таким композитным материалом, то следует доверить это профессионалам. Компания ИнноваСтрой уже много лет успешно осуществляет проекты по возведению объектов разной сложности.
Нашей фирме по силам любые задачи: начиная от проектирования постройки до сдачи готового объекта с отделкой. Что касается углеволокна, то это очень дорогой материал, который требует определенных навыков его монтажа, а также наличие специального оборудования. Для успешного выполнения армирования следует подготовить поверхность и сам композитный материал, правильно осуществить его монтаж (что зависит от типа конструкции), а затем грамотно нанести следующие слои.
ИнноваСтрой готова взяться за весь спектр работ по армированию постройки, а также выполнить ремонтные работы уже готовых сооружений с укреплением их карбоном. Мы работаем в строительной сфере уже не первый год и знаем территориальные особенности каждого региона, а потому сможем рассчитать целесообразное количество материала.
Сотрудничество домов и коттеджей с нами является гарантией таких преимуществ:
- Мы можем проводить встречи с клиентами удаленно. Данная функция наиболее выгодна, когда у заказчика нет возможности посетить наш офис лично. В таком случае, мы предлагаем связь по Скайпу или посредством другой удобной программы.
- Приемлемые цены на услуги строительной компании. Стоимость наших работ всегда очень разумна и рассчитывается исходя из определенных критериев.
- Индивидуальный подход. Каждый клиент очень ценен для нас, потому мы выслушиваем все ваши требования или пожелания по проекту и выполняем работу так, как было согласовано.
- Широкий спектр предоставляемых услуг. Наш штат имеет квалифицированных специалистов из разных отраслей строительства и отделки помещений.
Убедиться в нашем профессионализме вы можете, связавшись с менеджером компании по телефону. Мы с радостью ответим на все ваши вопросы и предоставим консультацию. Настало время заказать индивидуальный проект дома и получить жилье своей мечты!
innstroy.ru
Углеродное волокно Википедия
Углеродное волокно — материал, состоящий из тонких нитей диаметром от 5 до 15 мкм, образованных преимущественно атомами углерода. Атомы углерода объединены в микроскопические кристаллы, выровненные параллельно друг другу. Выравнивание кристаллов придает волокну большую прочность на растяжение. Углеродные волокна характеризуются высокой силой натяжения, низким удельным весом, низким коэффициентом температурного расширения и химической инертностью.
Углеродное волокно Углеродная лентаИстория[ | код]
Впервые получение и применение углеродных волокон было предложено и запатентовано в 1880 г. американским изобретателем Эдисоном для нитей накаливания в электрических лампах. Эти волокна получались в результате пиролиза хлопкового или вискозного волокна и отличались высокой пористостью и хрупкостью.
Вторично интерес к углеродным волокнам появился, когда велись поиски материалов, пригодных для использования в качестве компонентов для изготовления ракетных двигателей. Углеродные волокна по своим качествам оказались одними из наиболее подходящих для такой роли армирующими материалами, поскольку они обладают высокой термостойкостью, хорошими теплоизоляционными свойствами, коррозионной стойкостью к воздействию газовых и жидких сред, высокими удельными прочностью и жёсткостью.
Углеродное волокно 3К, 12К, 24КВ 1958 г. в США были получены УВ на основе вискозных волокон. При изготовлении углеродных волокон нового поколения применялась ступенчатая высокотемпературная обработка гидратцеллюлозных (ГТЦ) волокон (900 °C, 2500 °C), что позволило достичь значений предела прочности при растяжении 330—1030 МПа и модуля упругости 40 ГПа. Несколько позднее (в 1960 г.) была предложена технология производства коротких монокристаллических волокон («усов») графита с прочностью 20 ГПа и модулем упругости 690 ГПа. «Усы» выращивались в электрической дуге при температуре 3600 °C и давлении 0,27 МПа (2,7 атм). Совершенствованию этой технологии уделялось много времени и внимания на протяжении ряда лет, однако в настоящее время она применяется редко ввиду своей высокой стоимости по сравнению с другими методами получения углеродных волокон.
Почти в то же время в СССР и несколько позже, в 1961 г., в Японии были получены УВ на основе полиакрилонитрильных (ПАН) волокон. Характеристики первых углеродных волокон на основе ПАН были невысоки, но постепенно технология совершенствовалась и уже через 10 лет (к 1970 г.) были получены углеродные волокна на основе ПАН-волокон с пределом прочности 2070 МПа и модулем упругости 480 ГПа. Тогда же была показана возможность получения углеродных волокон по этой технологии с ещё более высокими механическими характеристиками: модулем упругости до 800 ГПа и пределом прочности более 3 ГПа. УВ на основе нефтяных пеков были получены в 1970 г. также в Японии.
Углеродная ткань плотностью 200 гр/м2Чэнь и Чун исследовали эффект углеродного волокна с добавкой кремнезема на усадку при высыхании бетона и пришли к выводу, что объемное соотношение углеродного волокна в количестве 0,19% (при средней длине волокна 5мм и диаметре 10 мкм) с отношением микрокремнезема, равным 15% от массы цемента, вызывало снижение усадки при высыхании до 84%. Исследователи обнаружили, что использование углеродного волокна с микрокремнеземом позволяет улучшить такие свойства, как прочность при сжатии и химическая стойкость[1].
Алхадиси Абдул Кадир и др. исследовали влияние добавки углеродного волокна на механические свойс
ru-wiki.ru
Углеволокно - Википедия
Материал из Википедии — свободной энциклопедии
(перенаправлено с «»)Текущая версия страницы пока не проверялась опытными участниками и может значительно отличаться от версии, проверенной 11 апреля 2016; проверки требуют 12 правок. Текущая версия страницы пока не проверялась опытными участниками и может значительно отличаться от версии, проверенной 11 апреля 2016; проверки требуют 12 правок.Углеродное волокно — материал, состоящий из тонких нитей диаметром от 5 до 15 мкм, образованных преимущественно атомами углерода. Атомы углерода объединены в микроскопические кристаллы, выровненные параллельно друг другу. Выравнивание кристаллов придает волокну большую прочность на растяжение. Углеродные волокна характеризуются высокой силой натяжения, низким удельным весом, низким коэффициентом температурного расширения и химической инертностью.
История[ | ]
Впервые получение и применение углеродных волокон (УВ) (точнее, нитей) было предложено и запатентовано известным американским изобретателем — Томасом Эдисоном — в 1880 г. в качестве нитей накаливания в электрических лампах. Эти волокна получались в результате пиролиза хлопкового или вискозного волокна и отличались хрупкостью и высокой пористостью и впоследствии были заменены вольфрамовыми нитями. В течение последующих 20 лет он же предложил получать углеродные и графитированные волокна на основе различных природных волокон.
Вторично интерес к углеродным волокнам появился в середине XX в., когда велись поиски материалов, пригодных для использования в качестве компонентов композитов для изготовления ракетных двигателей. УВ по своим качествам оказались одними из наиболее подходящих для такой роли армирующими материалами, поскольку они обладают высокой термостойкостью, хорошими теплоизоляционными свойствами, коррозионной стойкостью к воздействию газовых и жидких сред, высокими удельными прочностью и жёсткостью.
В 1958 г. в США были получены УВ на основе вискозных волокон. При изготовлении углеродных волокон нового поколения применялась ступенчатая высокотемпературная обработка гидратцеллюлозных (ГТЦ) волокон (900 °C, 2500 °C), что позволило достичь значений предела прочности при растяжении 330—1030 МПа и модуля упругости 40 ГПа. Несколько позднее (в 1960 г.) была предложена технология производства коротких монокристаллических волокон («усов») графита с прочностью 20 ГПа и модулем упругости 690 ГПа. «Усы» выращивались в электрической дуге при температуре 3600 °C и давлении 0,27 МПа (2,7 атм). Совершенствованию этой технологии уделялось много времени и внимания на протяжении ряда лет, однако в настоящее время она применяется редко ввиду своей высокой стоимости по сравнению с другими методами получения углеродных волокон.
Почти в то же время в СССР и несколько позже, в 1961 г., в Японии были получены УВ на основе полиакрилонитрильных (ПАН) волокон. Характеристики первых углеродных волокон на основе ПАН были невысоки, но постепенно технология совершенствовалась и уже через 10 лет (к 1970 г.) были получены углеродные волокна на основе ПАН-волокон с пределом прочности 2070 МПа и модулем упругости 480 ГПа. Тогда же была показана возможность получения углеродных волокон по этой технологии с ещё более высокими механическими характеристиками: модулем упругости до 800 ГПа и пределом прочности более 3 ГПа. УВ на основе нефтяных пеков были получены в 1970 г. также в Японии.
Получение[ | ]
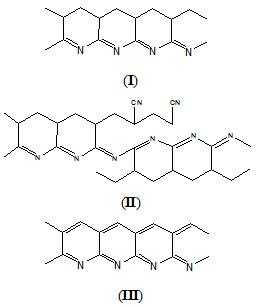
Рис. 1. Структуры, образующиеся при окислении ПАН-волокна
УВ обычно получают термической обработкой химических или природных органических волокон, при которой в материале волокна остаются главным образом атомы углерода. Температурная обработка состоит из нескольких этапов. Первый из них представляет собой окисление исходного (полиакрилонитрильного, вискозного) волокна на воздухе при температуре 250 °C в течение 24 часов. В результате окисления образуются лестничные структуры, представленные на рис. 1. После окисления следует стадия карбонизации — нагрева волокна в среде азота или аргона при температурах от 800 до 1500 °C. В результате карбонизации происходит образование графитоподобных структур. Процесс термической обработки заканчивается графитизацией при температуре 1600-3000 °C, которая также проходит в инертной среде. В результате графитизации количество углерода в волокне доводится до 99 %. Помимо обычных органических волокон (чаще всего вискозных и полиакрилонитрильных), для получения УВ могут быть использованы специальные волокна из фенольных смол, лигнина, каменноугольных и нефтяных пеков.
Дополнительная переработка УВ[ | ]
Углеродные волокна могут выпускаться в разнообразном виде: штапелированные (резаные, короткие) нити, непрерывные нити, тканые и нетканые материалы. Наиболее распространенный вид продукции — жгуты, пряжа, ровинг, нетканые холсты. Изготовление всех видов текстильной продукции производится по обычным технологиям, так же как для других видов волокон. Вид текстильной продукции определяется предполагаемым способом исп
encyclopaedia.bid
Углеволокно — материал будущего для строительства и ремонта
26 Августа 2015Углеродное волокно — современный материал, который состоит из тончайших нитей диаметром 5-15 микрометров, образованных в основном атомами углерода. Атомы объединены в мельчайшие кристаллы, расположенные параллельно друг другу. Благодаря такому выравниванию кристаллов углеволокно обладает значительной прочностью на растяжение.
Кроме того, этот материал имеет небольшой удельный вес и низкий коэффициент температурного расширения.
Еще одно ценное свойство углеволокна — его химическая инертность.
Сегодня углеродное волокно получают путем термической обработки синтетических или природных органических волокон, после чего в материале остаются главным образом атомы углерода.
Углеволокна бывают штапелированные — в виде коротких нитей; они могут представлять собой непрерывные нити, тканые и нетканые материалы, жгуты, пряжу.
Сферы применения углеволокна
Впервые углеродное волокно было получено и применено в 1880 году Томасом Эдисоном — он сделал из него нить накаливания для электрической лампочки. Позже стали использовать вольфрамовую нить накаливания.
Вновь об углеволокне вспомнили в середине ХХ века в связи с развитием ракетостроения; этот материал явился одним из элементов композитов для изготовления ракетных двигателей.
В наши дни углеродное волокно широко применяется в самолетостроении. Из него производят детали для электро- и радиотехники; экраны, поглощающие электромагнитное излучение; «карбоновые нагреватели», согревающие одежду и обувь; спортинвентарь.
В медицине углеволокно используется для очистки крови, для лечения ожогов, диабетических язв.
Применение углеволокна в строительстве
В строительстве углеволокно применяется для наружного армирования и для усиления конструкций — в качестве армирующего наполнителя, обладающего значительной устойчивостью к деформациям, а также к трещинам при резких перепадах температур.
Для усиления конструкций применяют также металл и бетон, но углеволокно обладает рядом преимуществ перед ними. Главное из них — высокая прочность на растяжение. Другие плюсы — существенное уменьшение веса усиливаемой конструкции и обеспечение ее коррозионной стойкости.
Углеволокно можно использовать для усиления конструкций из бетона, стали и древесины. Усиленный элемент приобретает дополнительно до 120 % прочности на сжатие и до 65 % прочности на изгиб.
Усиление колонн и перекрытий, упрочнение мостов — варианты применения композитов на основе углеволокна в строительстве, кажется, неисчерпаемы.
Для повышения прочности стен зданий в сейсмоопасных зонах можно применять внешнее армирование кирпичной кладки углеволокнистой тканью.
Применение углеволокна при ремонте и реставрации
Реставрация памятников архитектуры — это проблема всех старинных городов, в том числе и Тулы.
При обследовании объекта, подлежащего реставрации, как правило, выясняется, что кроме восстановления фасада необходимо выполнить работы по усилению несущих и ограждающих конструкций здания. В опорных сечениях деревянных балок зачастую образуются усушечные продольные трещины. Простым, эстетичным и щадящим конструкцию способом усиления таких балок является поверхностное наклонное армирование опорных зон боковых граней лентой из углеволокна.
Этот материал незаменим и при ремонте зданий и сооружений. Благодаря ему десятки объектов получили вторую жизнь без «хирургического вмешательства». Вместо раздалбливания пустот в плитах и металических кастетов на колоннах — изящные, практически невидимые бандажи из углеволокна. Вместо окольцовок зданий массивными швеллерами — легкие «повязки» из углеволокна. И всё это — без остановки производств и без отселения жильцов, с гарантированной долгой жизнью «вылеченной» конструкции.
А техническая мысль идет и идет вперед. Для углеволокна находятся все новые сферы применения. Так что за ним — будущее!
proftula.ru
Как изготовляют углеволокно? | Справочник рыболова, энциклопедия рыболова от F Гид
Начиналось всё с теории о том, что нужно взять уже готовую углеродную цепочку или искусственное волокно, которое в процессе обработки преобразуется в углерод. Поиски такого волокна продолжались несколько лет…
Лучшие результаты показали следующие материалы:
-
Волокна полиакрилонитриловые (PAN) ;
-
Волокна полученные методом протяжки расплавленного угольного, нефтяного или полихлорвинилового пака через сетку. Пак — это вид ароматичных смол.
Процесс изготовления углеволокна заключается в долговременном нагревании при различных температурах от 30 до 1500 градусов Цельсия, которое приводит к процессу пиролиза. Из материала убывают летучие составляющие, частички волокон образуют новые связи. Процентное содержание углерода в материале всё время увеличивается происходит процесс карбонизации. Одновременно с этим всё больше волокон преобразуется в чистые углеродные цепочки. Полученные волокна называются «carbon fibers» и обладают такими характеристиками, как прекрасная упругость и большая нагрузка на разрыв. Процесс завершается, когда эти параметры достигнут желаемого уровня.
В данный момент Вы читаете статью "Как изготовляют углеволокно?". Вас также могут заинтересовать другие статьи на тему "Бланк спиннинга" в Энциклопедии рыбалки.
Энциклопедия рыбалки - это раздел на сервисе F.Дневник, который содержит огромное количество статей о рыбалке. Здесь Ваш рыболовный гид F.Гид публикует советы рыболовных гидов, детальные статьи об эффективных способах ловли и снастях для рыбалки.
Энциклопедия о рыбалке - это также каталог рыб наших вод, в котором размещены подробные описания, условия обитания, привычки питания популярных объектов ловли: щуки, леща, судака, окуня, карпа, карася, сома, плотвы и многих других. Каждый рыбак найдет в нашей подборке статей о рыбалке что-то полезное. Благодаря детальным описаниям особенностей рыболовных снастей и приманок выбирайте самые уловистые воблеры, блесны, спиннербейты.
Читайте о технике ловли на спиннинг, фидер и на удочку. Изучайте историю и теорию рыбалки ради будущих рекордных уловов. А также проверяйте F.Прогноз рыбалки - первый в сети математически обоснованный прогноз клева рыбы, данные для которого взяты из реальных отчетов по рыбалке. Подсекай с F.Гид! F.Гид - Ваш рыболовный гид.
www.fgids.com